Links to external sources may no longer work as intended. The content may not represent the latest thinking in this area or the Society’s current position on the topic.
A cracking approach to inventing tough new materials: fracture stranger than friction
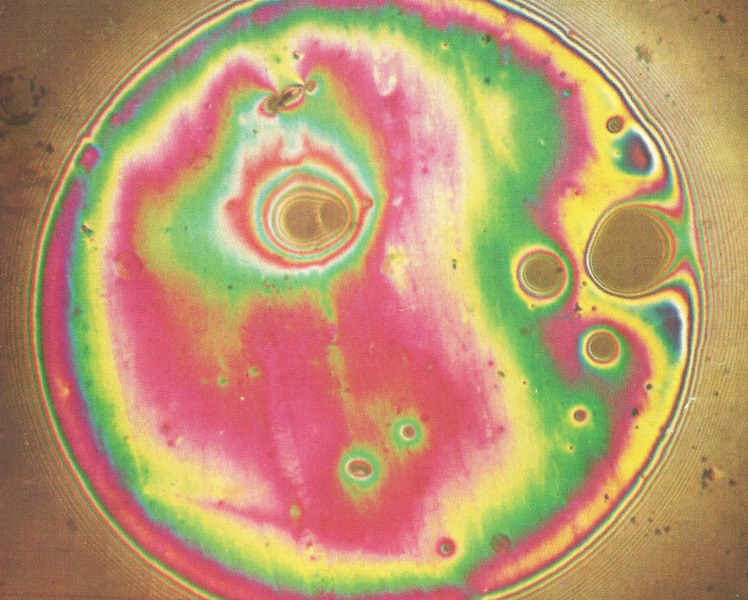
Online discussion meeting organised by Dr Kevin Kendall FRS, Professor Anthony Kinloch FREng FRS, Professor William Clegg and Dr Siva Bohm.
In the 100 years since Griffith published his ground-breaking paper on the energy criterion for cracking, there have been great advances in the understanding of cracks. This meeting reflected on recent observations in the field plus interesting new theories of cracking, as well as discussing how to invent tough new materials, while removing problems in Fracture Mechanics.
Please click on the YouTube link to view the recording of the event.
Enquiries: contact the Scientific Programmes team
Organisers
Schedule
13:00 - 13:09 |
Welcome by the Royal Society, Professor Julia Yeomans and Dr Kevin Kendall
It is almost exactly one century since Alan Arnold Griffith first presented his novel theory and experiments cracking glass on 21 October 1920, subsequently published in January 1921 in Philosophical Transactions of the Royal Society. The problem is that many engineers still use Galilean theory that stress causes cracking, whereas we now know for certain that Griffith energy equilibrium is the key, and the elastic stress field often has no influence on driving cracks. In other words, stress intensity factor does not exist in many fracture configurations. Therefore, the objectives for today are threefold 1) To celebrate the centenary of the original Griffith paper Today, we must reject ‘strength of brittle materials’ and use ‘toughness’ (ie fracture surface energy) as the determinant of cracking. ![]() Dr Kevin Kendall FRS, Adelan Ltd, UK
![]() Dr Kevin Kendall FRS, Adelan Ltd, UKKevin Kendall gained his PhD from the Cavendish Laboratory in 1970 for studies of contact and friction supervised by Professor David Tabor FRS. He then worked at British Railways in Derby on adhesion of iron oxide nanoparticles and became interested in fracture of adhesive joints, co-authoring the JKR paper with Johnson and Roberts. After post-docs in Australia and USA, he joined ICI in Runcorn and continued to pursue both theory and application of particle adhesion and cracking of polymers, cements and ceramics. Later he was Professor at Keele and Birmingham, where he started the ceramic fuel cell spin-out company Adelan Ltd, based on thermal-shock resistant zirconia. |
---|---|
13:09 - 13:17 |
Fracture toughness of 1D/2D-nanoreinforced cement via scratch testing
Cement is the most widely consumed material in the world, and the cement industry accounts for 7% of human-caused greenhouse gas emissions. A major scientific challenge is to devise enhanced-performance cement-based composites with a reduced carbon footprint. Nanomaterials offer the opportunity to improve mechanical characteristics, incorporate multifunctionality, and yield lightweight composites. This study investigates the fracture response of Portland cement reinforced with 1D and 2D carbon-based nanomaterials with a focus on carbon nanofibers, multiwalled carbon nanotubes, helical carbon nanotubes, and graphene oxide nanoplatelets. Scratch testing is used to probe the fracture parameters. In each test, a sphero-conical probe is pushed against the surface of the material under a linearly increasing vertical force, while recording the corresponding horizontal force and penetration depth. A novel model is formulated to measure the critical energy release rate via scratch testing using advanced nonlinear fracture mechanics. A significant increase in fracture toughness is observed in nano-reinforced cement and the dominating toughening mechanisms are nanofiller phase pulling out and crack bridging. Some additional mechanisms include capillary pore reduction and pore refinement. Thus, this study illustrates the potential of nanomaterials to toughen cement matrices while increasing the strength-to-weight ratio. ![]() Professor Ange-Therese Akono, Northwestern University, USA
![]() Professor Ange-Therese Akono, Northwestern University, USADr Ange-Therese Akono is an Assistant Professor in the Department of Civil and Environmental Engineering and the Department of Mechanical Engineering at Northwestern University. Dr Akono holds a PhD and an MSc from the Massachusetts Institute of Technology, USA, along with an MSc from the École Polytechnique, France. Dr Akono’s honours include the ASCE EMI Leonardo da Vinci Award, the National Center for Supercomputing Applications Faculty Fellowship, the ASCE New Faces of Civil Engineering Professionals Award, and the MIT Energy Initiative Fellowship. Dr Akono’s laboratory investigates fracture and failure mechanisms in complex materials systems at the molecular and nanometre length-scales. This interdisciplinary research is articulated over four main thrusts: multifunctional materials, green concrete, subsurface energy systems and biomaterials. |
13:17 - 13:19 |
Q and A
![]() Professor Ange-Therese Akono, Northwestern University, USA
![]() Professor Ange-Therese Akono, Northwestern University, USADr Ange-Therese Akono is an Assistant Professor in the Department of Civil and Environmental Engineering and the Department of Mechanical Engineering at Northwestern University. Dr Akono holds a PhD and an MSc from the Massachusetts Institute of Technology, USA, along with an MSc from the École Polytechnique, France. Dr Akono’s honours include the ASCE EMI Leonardo da Vinci Award, the National Center for Supercomputing Applications Faculty Fellowship, the ASCE New Faces of Civil Engineering Professionals Award, and the MIT Energy Initiative Fellowship. Dr Akono’s laboratory investigates fracture and failure mechanisms in complex materials systems at the molecular and nanometre length-scales. This interdisciplinary research is articulated over four main thrusts: multifunctional materials, green concrete, subsurface energy systems and biomaterials. |
13:19 - 13:27 |
Graphene production by cracking
Graphene, with its impermeability, high conductivity, and large strength to weight ratio, is considered a promising material for industrial application. Many industries have thus started to pursue graphene materials on a scale of tens or hundreds of thousands of square meters for numerous applications. The current bottlenecks for commercialisation these graphene applications are the availability of cost-effective, high-quality Graphene & Graphene oxide and its effective incorporation (functionalisation and dispersion) into commercial products in Automotive, Aerospace & Construction applications. Top-down routes of graphene production (i.e. graphite to graphene) can be both industrially scalable and cost-effective. What is required is that the energy needed to overcome interaction between graphene layers in graphite compensates by the overall energy change in the system that graphene layers evenly dispersed and stabilised. There are numerous ways to provide the required energy, namely chemical or electrochemical energy, high pressure, or mechanical forces. Incorporation of graphene into commercial products is facilitated by chemical modification of graphene platelets, tailored according to the application. ![]() Dr Sivasambu Bohm, Imperial College London, UK
![]() Dr Sivasambu Bohm, Imperial College London, UKDr Sivasambu Bohm received his first degree in Chemical Engineering, followed by an MSc at Hahn Meitner Institute (Max Planck Institute) in Berlin. After gaining his PhD at the University of Bath in Chemistry, he worked at different academic institutions, University of Swansea, TU Delft, The University of Birmingham and India Institute of Technology, Bombay. Siva has 20 years of industrial experience (TATA, Talga, CAMI and AM) in various research fields; metallurgy, protective coatings, energy storage in the automotive industry, smart coatings and nanotechnology, synthesis and applications of graphene. Dr Bohm has published 30 patents and 94 scientific publications. He is a Fellow of the Royal Society of Chemistry and a Fellow of Technical Surface Coatings. Dr Bohm has been awarded the Royal Society Industry Fellowship initial at University of Cambridge, Cambridge Graphene Centre. Since 2020, Dr Bohm has been completing his final year of a fellowship at Imperial College London and AM Commercial UK Ltd. |
13:27 - 13:29 |
Q and A
![]() Dr Sivasambu Bohm, Imperial College London, UK
![]() Dr Sivasambu Bohm, Imperial College London, UKDr Sivasambu Bohm received his first degree in Chemical Engineering, followed by an MSc at Hahn Meitner Institute (Max Planck Institute) in Berlin. After gaining his PhD at the University of Bath in Chemistry, he worked at different academic institutions, University of Swansea, TU Delft, The University of Birmingham and India Institute of Technology, Bombay. Siva has 20 years of industrial experience (TATA, Talga, CAMI and AM) in various research fields; metallurgy, protective coatings, energy storage in the automotive industry, smart coatings and nanotechnology, synthesis and applications of graphene. Dr Bohm has published 30 patents and 94 scientific publications. He is a Fellow of the Royal Society of Chemistry and a Fellow of Technical Surface Coatings. Dr Bohm has been awarded the Royal Society Industry Fellowship initial at University of Cambridge, Cambridge Graphene Centre. Since 2020, Dr Bohm has been completing his final year of a fellowship at Imperial College London and AM Commercial UK Ltd. |
13:29 - 13:37 |
Toughening materials: enhancing resistance to fracture
The ability of a material to undergo limited deformation is a critical aspect of conferring toughness as this feature enables the local dissipation of high stresses which would otherwise cause fracture. The mechanisms of such deformation can be diverse. Although plasticity from dislocation motion in crystalline materials is most documented, inelastic deformation can also occur via the sliding of mineralized collagen fibrils in tooth dentin and bone, rotation of such fibrils in skin, and even by mechanisms that also lead to fracture such as shear banding in glasses and microcracking in bone. Resistance to fracture (toughness) is thus a compromise - a combination of two, often mutually exclusive, properties of strength and ductility. It can also be considered as a mutual competition between intrinsic damage processes that operate ahead of the tip of a crack to promote its advance and extrinsic crack-tip shielding mechanisms that act mostly behind the crack tip to locally diminish crack-tip stresses and strains. Here the interplay between strength and toughness and between intrinsic and extrinsic mechanisms in developing toughness is examined in natural materials, (skin and bone), ceramic composites, and new metallic alloys (bulk-metallic glasses and high-entropy alloys). ![]() Professor Rob Ritchie FREng ForMemRS, University of California, Berkeley, USA
![]() Professor Rob Ritchie FREng ForMemRS, University of California, Berkeley, USARobert O Ritchie is the H.T. & Jessie Chua Distinguished Professor of Engineering in the Departments of Materials Science & Engineering and Mechanical Engineering at the University of California in Berkeley, and Senior Faculty Scientist at the Lawrence Berkeley National Laboratory. Prior to joining Berkeley in 1981, he was Associate Professor of Mechanical Engineering at MIT. He received MA, PhD and ScD degrees all from Cambridge University. He is known for his research into the mechanics and mechanisms of fracture and fatigue in a broad range of structural and biological materials. His current interests are focused on high-entropy alloys and bulk-metallic glasses, the mechanical properties of natural materials, including skin and bone, and the development of bioinspired structural materials. He is a member of the US National Academy of Engineering. |
13:37 - 13:39 |
Q and A
![]() Professor Rob Ritchie FREng ForMemRS, University of California, Berkeley, USA
![]() Professor Rob Ritchie FREng ForMemRS, University of California, Berkeley, USARobert O Ritchie is the H.T. & Jessie Chua Distinguished Professor of Engineering in the Departments of Materials Science & Engineering and Mechanical Engineering at the University of California in Berkeley, and Senior Faculty Scientist at the Lawrence Berkeley National Laboratory. Prior to joining Berkeley in 1981, he was Associate Professor of Mechanical Engineering at MIT. He received MA, PhD and ScD degrees all from Cambridge University. He is known for his research into the mechanics and mechanisms of fracture and fatigue in a broad range of structural and biological materials. His current interests are focused on high-entropy alloys and bulk-metallic glasses, the mechanical properties of natural materials, including skin and bone, and the development of bioinspired structural materials. He is a member of the US National Academy of Engineering. |
13:39 - 13:45 |
Cracking of adhesive contact between rubber spheres
In 1970, Alan Roberts studied rubber windscreen-wipers for his PhD. To avoid the variable roughness on commercial wipers, he invented a way to mould the hot rubber in a glass concave lens to form an optically smooth and reproducible surface. He took a wedge of raw rubber and inserted it into a smooth glass former, then hot-pressed it to crosslink the polymer. Contact between this surface and glass was excellent and the interference fringes could then be measured precisely. In 1966, Alan first saw that the contact of the dry smooth rubber on glass was much bigger than that on wet glass. Then in soapy water, the spot size was much smaller. Because a point contact is much easier experimentally than a windscreen wiper, and also because the Hertz elastic contact theory is for sphere contacts, Alan began to mould optically smooth rubber spheres to compare directly with the equation. From the plot of theory versus experimental results, the soapy water contact size fitted the Hertz theory, but the dry black spots were much bigger. Ken Johnson had obtained the stress field solution for adhering spheres much earlier by adding the well-known Hertz and Boussinesq stress distributions in 1958. He then observed the infinite stress giving a crack at the edge of this combined contact but failed to consider the Griffith energy argument to analyse the crack equilibrium. Twelve years later, Kendall realised that it was necessary to apply Griffith’s energy balance. The energy balance gave the JKR equation which showed that the Hertz equation needed three more terms to fit the results. The moral of this paper is that stress analysis by itself cannot give the condition for cracking. The stress distributions must be used to work out the energy balance principle that Griffith proposed in 1920. Then the new JKR equation emerges, fitting the experimental results for equilibrium. This JKR solution is much different from the famous Griffith equation for cracking sheets, showing that various particular solutions to the Griffith energy conservation principle must be considered. ![]() Dr Payal Baheti, Aston University, UK
![]() Dr Payal Baheti, Aston University, UKPayal gained her MSc Chemistry in India (2015) and then a co-tutelle PhD from the University of Nottingham, UK and ENSCM, France in 2019 for the studies of Sustainable Polymers and scCO2 mentored by Professor Steve Howdle and Professor Patrick Lacroix-Desmez. In May 2019, she joined the Aston University as ERDF Research Associate to support the delivery of the project - Enabling Technologies and Innovation Competencies Challenge that offers scientific as well as business assistance to local Small-to-Medium Enterprises. She has successfully delivered assistance to enterprises in sectors including building materials, renewable recyclable materials, cosmetics, packaging, healthcare and wellbeing, sports fabric and textile, UVR Visor as well as supporting NGOs. |
13:45 - 13:47 |
Q and A
![]() Dr Payal Baheti, Aston University, UK
![]() Dr Payal Baheti, Aston University, UKPayal gained her MSc Chemistry in India (2015) and then a co-tutelle PhD from the University of Nottingham, UK and ENSCM, France in 2019 for the studies of Sustainable Polymers and scCO2 mentored by Professor Steve Howdle and Professor Patrick Lacroix-Desmez. In May 2019, she joined the Aston University as ERDF Research Associate to support the delivery of the project - Enabling Technologies and Innovation Competencies Challenge that offers scientific as well as business assistance to local Small-to-Medium Enterprises. She has successfully delivered assistance to enterprises in sectors including building materials, renewable recyclable materials, cosmetics, packaging, healthcare and wellbeing, sports fabric and textile, UVR Visor as well as supporting NGOs. |
13:47 - 13:51 |
Calculations on compact disc cracking
The Griffith equation σ= {EW/𝝅c}1/2 where σ is equilibrium cracking stress, E is Young’s modulus, W is fracture surface energy, and c is crack length, has three problems. First, it applies to an infinite sheet whereas a lab test sample is typically near 100 x 100 mm. Second, it applies to a central crack instead of the more dangerous and easily observable edge crack. Third, the theory assumes a uniform stress field, instead of tensile force application normally used in the laboratory. The purpose of this presentation is to calculate the crack behaviour of PMMA (poly methyl meth acrylate) discs, pin loaded in tension to avoid all three issues. Ronald Douglas Gregory produced an exact theory of disc cracking in 1979. He showed that his new equation based on the Griffith energy conservation principle could fit some experimental cracking results on PMMA, although experimental tests of his equation have not been common.
Calculation showed that axial disc loading gave nominal strength results comparable with Griffith theory but more acceptable because the force went to zero as the crack fully crossed the disc. The Galilean concept strength= force/area prediction was only correct at the intrinsic flaw length around 0.013mm. ![]() Mr Kaan Kendall, King Edward VI Five Ways Sixth Form
![]() Mr Kaan Kendall, King Edward VI Five Ways Sixth FormA Sixth Form student working on fracture mechanics and trying to prove the Griffith theory wrong for good.
|
13:51 - 13:53 |
Q and A
![]() Mr Kaan Kendall, King Edward VI Five Ways Sixth Form
![]() Mr Kaan Kendall, King Edward VI Five Ways Sixth FormA Sixth Form student working on fracture mechanics and trying to prove the Griffith theory wrong for good.
|
13:53 - 14:01 |
The dangers of single lap shear testing in understanding polymer composite welded joints
Single lap shear joints are straightforward to manufacture. This makes them especially attractive for testing polymer composite welded joints. Owing to local heating, which is characteristic of composite welding processes, the production of more geometrically intricate joints (such as double lap or scarfed joints) or bigger joints (such as end-notched flexural or double cantilever beam) typically entails a significant complexity in the design of the welding process. Testing of single lap shear joints is also uncomplicated and, even though, owing to mixed-mode loading and uneven stress distribution, it does not provide design values, it is widely acknowledged as a valuable tool for comparison. Even so, comparing different aspects of composite welded joints through their corresponding single lap shear strength values alone can be deceptive. In this presentation, results from various projects will show that comparison of different welding processes, adherend materials, process parameters or different types of joining techniques through single lap shear testing is only meaningful when strength values are combined with knowledge on other aspects of the joints such as stiffness, architecture and failure modes. ![]() Dr Irene Fernandez Villegas, Delft University of Technology, The Netherlands
![]() Dr Irene Fernandez Villegas, Delft University of Technology, The NetherlandsIrene Fernandez Villegas graduated as an Aerospace Engineer at the Poly-Technical University of Madrid (UPM). In 2005 she got a PhD degree from the same University on Resistance Welding of Thermoplastic Composites. She has more than 15 years of research experience on processing and welding of thermoplastic composites, first at the National Institute of Aerospace Engineering in Madrid and currently at the Delft University of Technology in the Netherlands, where she works as an Associate Professor. In the last 12 years the efforts of the research team led by Dr Fernandez Villegas at TU Delft have been strongly focused on understanding and developing ultrasonic welding of composite structures. Apart from her work on the development of welding technologies, Dr Fernandez Villegas is interested in exploring how to make use of these and other new technologies to design sustainable aircraft structures. |
14:01 - 14:03 |
Q and A
![]() Dr Irene Fernandez Villegas, Delft University of Technology, The Netherlands
![]() Dr Irene Fernandez Villegas, Delft University of Technology, The NetherlandsIrene Fernandez Villegas graduated as an Aerospace Engineer at the Poly-Technical University of Madrid (UPM). In 2005 she got a PhD degree from the same University on Resistance Welding of Thermoplastic Composites. She has more than 15 years of research experience on processing and welding of thermoplastic composites, first at the National Institute of Aerospace Engineering in Madrid and currently at the Delft University of Technology in the Netherlands, where she works as an Associate Professor. In the last 12 years the efforts of the research team led by Dr Fernandez Villegas at TU Delft have been strongly focused on understanding and developing ultrasonic welding of composite structures. Apart from her work on the development of welding technologies, Dr Fernandez Villegas is interested in exploring how to make use of these and other new technologies to design sustainable aircraft structures. |
14:03 - 14:07 |
Remove Fracture Mechanics Errors
Several ASTM standards on fracture of glued and welded joints need attention because they do not consider the Griffith energy criterion of cracking which was proposed a century ago. It is almost as if Griffith never existed because the ASTM definition of failure is the stress criterion postulated by Galileo in 1638 in which stress at failure, (ie Strength=Force/Area) is defined as the determinant of fracture. Irene Martinez Villegas shows in this volume that attempts to use ASTM D5868 to standardise welded composite (carbon fibre reinforced polymer CFRP) lap joints reveal major problems. First, the test is a low angle bend-peel test; not shear. Second, the energy required to break the joint is not emphasised so that joints may have high strength properties but also low toughness; Third, the fracture force is not proportional to the lap joint area so the concept of strength independent of sample size is false; fourth, as the CFRP panels are made thicker, the strength rises at constant overlap area so strength can be any value you want; fifth, the strength of larger joints goes down; this is the size effect noted in many bend-cracking tests, much as Galileo suggested for bent beam fracture in his famous book ‘the larger the machine, the greater its weakness’. The purpose of this paper is to demonstrate that poor ASTM ‘shear strength’ standards should be replaced by a definition of welded lap joint performance based on Griffith’s energy conservation argument in which fracture surface energy is the main parameter resisting failure. The foundation of this Griffith-style lap joint analysis for long cracks goes back to 1975 but has been largely ignored until now because it does not fit the Griffith equation for cracked sheets, has no ‘stress intensity factor’, and travels at constant speed, not accelerating like the standard Griffith tension crack. This study of tensile delamination shows that a long lap crack is not driven by stress near the crack but by changes in stored elastic energy in the stretched strips remote from the crack tip, while strain energy release rate is negative. It would be more appropriate to call this lap failure a tensile delamination crack rather than ‘shear strength’. ![]() Dr Kevin Kendall FRS, Adelan Ltd, UK
![]() Dr Kevin Kendall FRS, Adelan Ltd, UKKevin Kendall gained his PhD from the Cavendish Laboratory in 1970 for studies of contact and friction supervised by Professor David Tabor FRS. He then worked at British Railways in Derby on adhesion of iron oxide nanoparticles and became interested in fracture of adhesive joints, co-authoring the JKR paper with Johnson and Roberts. After post-docs in Australia and USA, he joined ICI in Runcorn and continued to pursue both theory and application of particle adhesion and cracking of polymers, cements and ceramics. Later he was Professor at Keele and Birmingham, where he started the ceramic fuel cell spin-out company Adelan Ltd, based on thermal-shock resistant zirconia. |
14:07 - 14:09 |
Q and A
![]() Dr Kevin Kendall FRS, Adelan Ltd, UK
![]() Dr Kevin Kendall FRS, Adelan Ltd, UKKevin Kendall gained his PhD from the Cavendish Laboratory in 1970 for studies of contact and friction supervised by Professor David Tabor FRS. He then worked at British Railways in Derby on adhesion of iron oxide nanoparticles and became interested in fracture of adhesive joints, co-authoring the JKR paper with Johnson and Roberts. After post-docs in Australia and USA, he joined ICI in Runcorn and continued to pursue both theory and application of particle adhesion and cracking of polymers, cements and ceramics. Later he was Professor at Keele and Birmingham, where he started the ceramic fuel cell spin-out company Adelan Ltd, based on thermal-shock resistant zirconia. |
14:09 - 14:25 | Discussion |
14:25 - 14:27 |
Conclusions
![]() Dr Kevin Kendall FRS, Adelan Ltd, UK
![]() Dr Kevin Kendall FRS, Adelan Ltd, UKKevin Kendall gained his PhD from the Cavendish Laboratory in 1970 for studies of contact and friction supervised by Professor David Tabor FRS. He then worked at British Railways in Derby on adhesion of iron oxide nanoparticles and became interested in fracture of adhesive joints, co-authoring the JKR paper with Johnson and Roberts. After post-docs in Australia and USA, he joined ICI in Runcorn and continued to pursue both theory and application of particle adhesion and cracking of polymers, cements and ceramics. Later he was Professor at Keele and Birmingham, where he started the ceramic fuel cell spin-out company Adelan Ltd, based on thermal-shock resistant zirconia. |