Links to external sources may no longer work as intended. The content may not represent the latest thinking in this area or the Society’s current position on the topic.
The challenges of hydrogen and metals
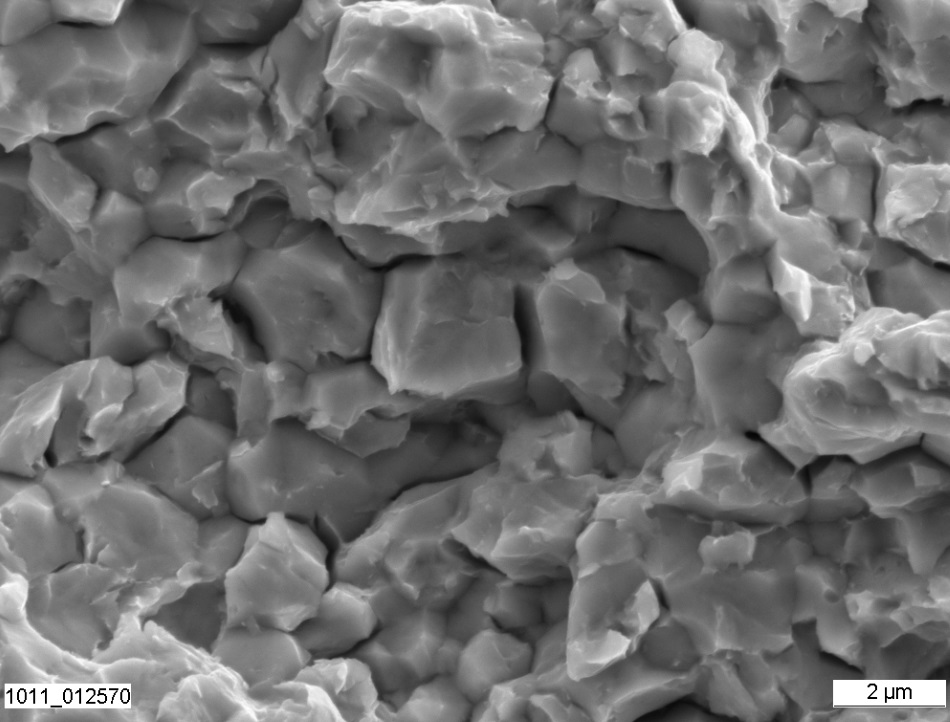
Scientific discussion meeting organised by Professor Anthony Paxton, Professor Michael Finnis and Professor Adrian Sutton FRS
Hydrogen produced from renewable energy promises clean transport. The challenge is to defeat hydrogen's pernicious effects on metals deployed in its handling and storage. “Hydrogen embrittlement” is a major concern for the automotive, construction and energy sectors. This meeting will focus on the fundamental science underpinning the harmful effects of hydrogen on metals, from quantum mechanics to fracture mechanics.
Audio recordings of the speakers can be found below. A special issue of Philosophical Transactions of the Royal Society A will be published in due course.
Enquiries: Contact the Scientific Programmes team.
Organisers
Schedule
09:00 - 09:50 |
Decarbonising the UK Gas Network – The H21 Project
The H21 Leeds City Gate project is a feasibility study developed by Northern Gas Networks (NGN). The project’s ambition is to establish if it is technically and economically possible to convert the existing natural gas supply in one of the largest UK cities (Leeds) to hydrogen. It has addressed where and how the hydrogen would be produced, how supply and demand would be managed and what would be the overall costs for the conversion. This project could be used as a blue print for a potential UK wide incremental rollout of a hydrogen gas system to decarbonise heat. ![]() Dan Sadler, Northern Gas Networks, UK
![]() Dan Sadler, Northern Gas Networks, UKA chartered Engineer with 17 years industry experience. Dan started on British Gas’s graduate training program progressing to project manager for high pressure gas pipelines and pressure reduction stations. In 2008 he joined Rhead Group, a professional services consultancy, in the role of as Divisional Director for Energy (UK). Dan joined Northern Gas Networks in 2012 as ‘Head of Investment Planning and Major Projects’ following supporting the network in their RIIO-GD1 submission. In late 2014 he became ‘Head of Energy Futures’ a role in which he developed and led the H21 Leeds City Gate project. Currently Dan has just returned (Jan 2017) to Northern Gas Networks as ‘Special Advisor’ following completion of a one year secondment to BEIS as ‘Technical advisor – Future of the Gas Networks’. |
|
---|---|---|
09:50 - 10:35 |
Clean energy and the hydrogen economy
In recent years, newfound interest in the hydrogen economy from both industry and academia has helped to shed light on its potential. Hydrogen can enable an energy revolution by providing much needed flexibility in renewable energy systems. As a clean energy carrier, hydrogen offers a range of benefits for simultaneously decarbonising the transport, residential, commercial and industrial sectors. Hydrogen is also shown to have synergies with other low carbon alternatives and can enable a more cost-effective transition to a de-carbonised and cleaner energy systems. This paper presents the opportunities for the use of hydrogen and fuel cells in each sector and identifies the benefits and challenges within the hydrogen supply chain for power-to-gas, power-to-power and gas-to-gas supply pathways. While, industry players have already started market introduction of hydrogen fuel cell systems, including fuel cell electric vehicles and micro-combined heat and power devices, the use of hydrogen at grid-scale requires the challenges of clean hydrogen production, bulk storage, and distribution to be resolved. Ultimately, greater government support, in partnership with industry and academia, is needed to realise hydrogen’s potential across all economic sectors. ![]() Professor Nigel Brandon OBE FREng, Imperial College London
![]() Professor Nigel Brandon OBE FREng, Imperial College LondonProfessor Nigel Brandon is an electrochemical engineer whose research interests are focussed on the science and engineering of electrochemical devices for energy applications, in particular fuel cells, batteries and electrolysers. He is Director of the Sustainable Gas Institute at Imperial College London, addressing the challenges and role of natural gas in the energy system, Director of the EPSRC funded Hydrogen and Fuel Cell SUPERGEN Hub, and Co-Director of the Energy SuperStore Hub. He is a founder of the fuel cell company Ceres Power, has published over 170 papers, and holds 15 patents. He has been awarded the Royal Academy of Engineering Silver Medal for his contribution to fuel cell engineering leading to commercial exploitation, and the ASME Francis Bacon Medal for his contribution to fuel cell science, engineering and education.
|
|
10:35 - 11:00 | Coffee | |
11:00 - 11:45 |
Effect of material characteristics on hydrogen embrittlement failures of high strength steel fasteners
High strength steel fasteners characterised by tensile strengths above 1 100 MPa are often used in critical applications where a failure can have catastrophic consequences. Preventing Hydrogen Embrittlement (HE) failure is a fundamental concern implicating the entire fastener supply chain. Research is typically conducted under idealised conditions that cannot be translated into know-how prescribed in fastener industry standards and practices. Additionally, inconsistencies and even contradictions in fastener industry standards have led to much confusion and many preventable or misdiagnosed fastener failures. The fact that HE is often mistakenly declared to be the root cause of failure as opposed to a mechanism of failure is a reflection of the confusion. HE susceptibility is a function of the material condition, which is comprehensively described by the metallurgical and mechanical properties. Material strength has a first order effect on HE susceptibility which increases significantly above 1 200 MPa and is characterised by a ductile-brittle transition. For a given concentration of hydrogen and at equal strength, the critical strength above which the ductile-brittle transition begins can vary due to second order effects of chemistry, tempering temperature and sub-microstructure. Additionally, non-homogeneity of the metallurgical structure resulting from poorly controlled heat treatment, impurities and non-metallic inclusions can increase the susceptibility of steel in ways that are measurable but unpredictable. This is the root cause of many real-life failures, some cases of which will be examined in this talk. ![]() Professor Salim Brahimi, Industrial Fasteners Institute, USA
![]() Professor Salim Brahimi, Industrial Fasteners Institute, USASalim Brahimi is president of IBECA Technologies Corp. and as of January 1, 2016, was appointed technical director at the Industrial Fasteners Institute (IFI). He is a licensed member of the Quebec Order of Professional Engineers. He has accumulated nearly 28 years of experience as a fastener and bolting professional. Mr. Brahimi also serves as chairman of ASTM Committee F16 on Fasteners, as head of the Canadian delegation to ISO Committee TC2 on Fasteners, as vice chair of the Research Council on Structural Connections (RCSC), and as member of ASME Committee B18 and the SAE Fastener Committee, and ASTM F07.04 on hydrogen embrittlement. Research Salim Brahimi and Prof. Stephen Yue co-founded the McGill University Hydrogen Embrittlement Facility (MHEF) in 2006 by as a collaborative research project, co-sponsored by industrial partners and the government of Canada. The ongoing research follows multiple tracks: (i) fastener materials susceptibility, (ii) interactions of fastener materials with coatings and coating processes, and (ii) aerospace materials and coatings. 2015 – IFI Soaring Eagle Technology award: bestowed by the Industrial Fasteners Institute in recognition for “his past and on-going contribution to the fastener industry’s body of knowledge in the areas of materials and finishes, and their impact on hydrogen induced failures in high strength fasteners.” 2004 - Fred F. Weingruber award: bestowed by ASTM Committee F16 in recognition for “his outstanding contributions to the development of fastener standards, especially in the field of hydrogen embrittlement.” |
11:45 - 12:15 |
The first principles approach: insights into hydrogen trapping by microstructures in steels
Modern high strength steels contain a significant amount of precipitates and non-metallic inclusions. Their presence is often correlated to the sensitivity of the material to hydrogen embrittlement. The underlying assumption is that these particles strain the surrounding lattice and therewith promote the trapping of H in the interface. On the one hand, this increases the amount of diffusible and/or trapped H in the material. On the other hand, a resulting decohesion of the interfaces can yield crack initiation and therefore provides one of the possible mechanisms for hydrogen embrittlement. Experiments on H distribution based on atom probe tomography and of fracture surfaces (so-called fish-eyes) support these assumptions, but are typically not conclusive. In the presented work, the first principles methods is therefore used to simulate the interaction of H with precipitates. To understand the impact of chemical and mechanical contributions to H solution enthalpies in the interfaces, the role of iron-based carbides (Fe3C and Fe3AlC1-x), and titanium-based precipitates are compared. For perfect and coherent interfaces the trapping energies are generally found to be small, but a noticeable impact on decohesion energies is confirmed. The presence of vacancies in the interface substantially increases the hydrogen trapping. In the same way, the impact of misfit dislocations on H solubility has been considered in a semi-coherent approach. Different concepts to calculate the role of misfit dislocations are presented, using density functional theory (DFT) as well as tight-binding (TB) approaches. Such an extension of the H trapping investigation beyond the limited systems sizes accessible by DFT will form the last part of the presentation. The results obtained for precipitates with the H trapping at edge dislocations and grain boundaries will be compared. The insights can contribute to an optimization of microstructures such that their sensitivity to hydrogen embrittlement is reduced. ![]() Dr Tilmann Hickel, Max-Planck-Institut für Eisenforschung GmbH, Germany
![]() Dr Tilmann Hickel, Max-Planck-Institut für Eisenforschung GmbH, GermanyTilmann Hickel studied physics at Humboldt University Berlin, Germany, and Loughborough University, England, and finished his PhD in 2005 on many-body theories for magnetic materials. He afterwards joined the Max-Planck-Institut für Eisenforschung GmbH, where he became in 2006 head of the group “Computational phase studies” within the department “Computational Materials Design”. His group focuses on the ab initio based simulation of materials properties and phase stabilities at finite temperatures, with a particular focus on steels. |
|
---|---|---|
12:30 - 13:15 |
A kinetic Monte Carlo approach to diffusion controlled thermal desorption spectroscopy
Atomistic simulations of thermal desorption spectra (TDS) for effusion from bulk materials to characterize binding or trapping sites are a challenging task since large system sizes as well as extended time scales are required. A powerful tool to follow the dynamical evolution of an atomistic system on extended time scales are kinetic Monte Carlo (KMC) simulations. Combined with input data from electronic structure calculations KMC can e.g. provide detailed insight into the diffusion behaviour of hydrogen in iron for different microstructures. For diffusion controlled TDS of bulk samples KMC simulations can, however, become prohibitively expensive. In this presentation a method is introduced where KMC is combined with an analytic approximation of superbasins within the framework of absorbing Markov chains. The approach is applied to the effusion of hydrogen from bcc iron, where the diffusion within bulk grains is coarse grained using absorbing Markov chains, which provide an exact solution of the dynamics within a superbasin. The analytic approximation to the superbasins is transferable with respect to grain size and elliptical shapes and can be applied in simulations with constant temperature as well as constant heating rate. The resulting TDS are in close agreement with direct KMC simulations, but the calculations are computationally much more efficient. The presented approach is thus applicable to much larger system sizes and provides a first step towards an atomistic understanding of the influence of structural features on the position and shape of peaks in thermal desorption spectra. ![]() Dr Jutta Rogal, New York University, USA
![]() Dr Jutta Rogal, New York University, USAJutta Rogal is currently a Heisenberg Fellow of the German Research Foundation with a research appointment at the Department of Chemistry at New York University (NYU) and the Department of Physics at Freie Universität Berlin (FUB). She received her doctorate from FUB in 2006, carrying out her PhD work on electronic structure calculations for surface catalysis at the Fritz Haber Institute. For her PhD thesis, she was awarded the Otto Hahn Medal of the Max Planck Society and the Ernst-Reuter Preis of the FUB. In 2007, Jutta moved to the University of Amsterdam as a Postdoctoral Researcher to develop methodological extensions to the transition path sampling approach, before joining the Interdisciplinary Centre for Advanced Materials Simulation at the Ruhr University Bochum as Group Leader from 2009-2020. In 2016, she was awarded a Feodor Lynen Research Fellowship of the Alexander von Humboldt Foundation which she spent at NYU in 2017/18 working on enhanced sampling techniques for high-dimensional energy landscapes. |
|
13:15 - 14:15 | Lunch | |
14:15 - 15:00 |
The physics of hydrogen transport and trapping in metals
Interstitial lattice diffusion in the presence of any distribution of trap concentration and energy is treated in the framework of statistical thermodynamics, reaction rate theory and kinetic Monte Carlo simulations. Consequences for hydrogen regarding electrochemical permeation measurements and thermal desorption spectroscopy are discussed. It will be shown that the “free” or “diffusible” hydrogen can be defined exactly via the chemical potential of hydrogen as the thermodynamic activity of hydrogen. For hydrogen the nature of traps stemming from lattice defects is discussed in detail. Among these vacancies and metal/oxide-interfaces provide the deepest traps. ![]() Professor Reiner Kirchheim, University of Göttingen, Germany
![]() Professor Reiner Kirchheim, University of Göttingen, GermanyProfessor Reiner Kirchheim received his PhD in Physics from the University of Stuttgart in 1973. Until 1993 he worked as a senior research scientist at the Max-Plank-Institute for Metals Research in Stuttgart. He joined the faculty of Physics at the Georg-August-University Göttingen, where he became full professor in Materials Physics in 1993. From 1979 till 1998 he was visiting for longer periods of time Rice University, University of Illinois, Ohio State University and NIST as a post doc and visiting professor. Since 2009 he continues his work at the University of Göttingen as a Distinguished Professor of the state of Lower Saxony. In 2010 he was elected a member of the Max-Planck-Society and since 2011 he is also Principal Investigator at the World Premier International Institute for Carbon-Neutral Energy Research, Kyushu University, Japan. Prof. Kirchheim is known for his research in the field of thermodynamics, kinetics of materials and electrochemistry with special emphasis on hydrogen in metals, nanocrystalline alloys and amorphous materials. He is an elected member of the German National Academy of Technical Sciences and the Göttingen Academy of Science and has been a recipient of several other honors and awards (http://www.material.physik.uni-goettingen.de/index.php?site=kirchheim_info&lang=de). |
|
15:00 - 15:45 |
Isotopic tracing of hydrogen transport and trapping in nuclear materials
Some illustrations of the use of deuterium or tritium for isotopic tracing of hydrogen absorption, transport and trapping in nuclear materials are presented. Isotopic tracing of hydrogen has been shown to be successful for the determination of the boundaries conditions for hydrogen desorption or absorption in a material exposed to a hydrogen source. Also, the unique capabilities of isotopic tracing and related techniques to characterize H interactions with point defects and dislocations acting as moving traps has been demonstrated. Such transport mechanisms are considered to play a major role in some stress corrosion cracking and hydrogen embrittlement mechanisms. ![]() Dr Frantz Martin, CEA Saclay, France
![]() Dr Frantz Martin, CEA Saclay, FranceFrantz Martin received his PhD in Materials Science from University Pierre and Marie Curie, Paris, France, in 2005. His PhD works, supervised by of Pr. Philippe Marcus and Dr. Jacques Cousty, focused on the onset of localized corrosion of stainless steels in chloride environments, such as pitting and Stress Corrosion Cracking, by the way of Atom Probes. After a post-doctoral fellowship in the group of Prof. John Watts under the supervision of Prof. James E. Castle at University of Surrey, UK, Frantz joined the corrosion service at the CEA Saclay (French Research Center on Atomic Energy) by the end of 2006. His research started at CEA studying corrosion and hydrogen matters in deep geological storage conditions for nuclear waste, as well as works in continuity with his PhD concerns. In 2010 he became part of the research group lead by Jacques Chêne at CEA dedicated to hydrogen-material interactions studies. His current research is related with environmental degradation mechanisms of structural and functional materials, including Stress Corrosion Cracking and Hydrogen Embrittlement, with a particular interest in the isotopic tracing of hydrogen with deuterium and tritium. |
|
15:45 - 17:00 | Tea and networking |
09:00 - 09:45 |
Hydrogen related challenges for the steelmaker
The modern steelmaker of advanced high-strength steels has always been challenged with the conflicting targets of increased strength while maintaining or improving ductility. These new steels help the transportation sector, including that of automotive, achieve goals of increased passenger safety and reduced emissions. With increasing tensile strengths, certain steels exhibited an increased sensitivity towards hydrogen embrittlement. Characterizing the material’s sensitivity in as-delivered condition has been developed and accepted (SEP1970), but the complexity of the stress-states that can induce an embrittlement together with the wide range of applications for high strength steels make the development of a standardized test for hydrogen embrittlement under in-service conditions extremely challenging. Some proposals for evaluating the material’s sensitivity give an advantage to materials with a low starting ductility. In spite of this, newly developed materials can have a higher original elongation while suffering only a moderate reduction in elongation due to hydrogen. This work presents a characterization of new materials and their sensitivity towards hydrogen embrittlement. ![]() Dr Richard Thiessen, Thyssenkrupp Steel Europe, Germany
![]() Dr Richard Thiessen, Thyssenkrupp Steel Europe, GermanyRichard Thiessen studied Materials Engineering in Canada (University of Alberta), Computational Mechanics in Germany (University of Stuttgart), and completed his PhD in Materials Science from the TU Delft in 2006. His thesis proposed a multi-scale methodology for using physically-based phase-field simulations to understand the microstructure evolution during welding. After a period as post-doc at the Max-Planck-Institute for Iron Research where he investigated damage mechanisms in multi-phase steels, Richard joined the materials development team within R&D at thyssenkrupp Steel Europe in Duisburg, Germany (2007). Richard’s career at thyssenkrupp started with fundamental research topics such as hydrogen embrittlement and comparisons between lab conditions and industrial production, but soon led to development work on 3rd generation advanced high strength steels. He has managed several EU projects with topics ranging from the influence of microstructure on the susceptibility of steels towards hydrogen embrittlement to optimization of “quench and partitioning” steels for industrial applications. Currently Richard leads a group of engineers working on new steel concepts within the materials development team at Thyssenkrupp Steel Europe. |
|
---|---|---|
09:45 - 10:30 |
Hydrogen embrittlement in structural steels
Hydrogen embrittlement reduces both the ductility and toughness of steels, and such degradation of performance is important in a range of applications from energy storage in transport (hydrogen tanks in automobiles) to the energy supply industry (such as subsea pipelines that are exposed to hydrogen as a consequence of cathodic protection measures). In the first part of the presentation, it is argued that the reduction in strength and toughness by hydrogen is associated with the embrittlement of grain boundaries and other trapping sites for hydrogen. Elementary kinetic theory suggests that embrittlement is associated with trap binding energies in the range -20 to -30 kJ/mol at room temperature. In order to predict the reduction in macroscopic tensile strength due to the presence of hydrogen at grain boundaries, it is argued that the cohesive strength of the grain boundaries is reduced by hydrogen. This can be modelled in two ways: (i) macro-level: no elevation in local tensile stress at the grain boundary and the presence of hydrogen reduces the macroscopic cohesive strength to the order of the yield strength; (ii) meso-level: a stress raising defect (such as a short crack) exists at the grain boundary such that the local stress level much exceeds the yield strength; the presence of hydrogen reduces the cohesive strength but it remains much above the yield strength. In the second part of the talk, an analytical and numerical analysis is given of the electro-permeation test. This test is commonly used to measure the diffusion behaviour of hydrogen in engineering steels (and other alloys). There is no consensus in the literature on the values of trap binding energy and trap density for particular classes of trap, and this is in-part due to misinterpretation of permeation data, and by not varying the initial concentration of hydrogen over a sufficiently wide range. Our analysis reveals regimes of behaviour, and the resulting permeation map can be used to obtain a clear and unique interpretation of the data. ![]() Professor Norman Fleck FRS, University of Cambridge, UK
![]() Professor Norman Fleck FRS, University of Cambridge, UKNorman Fleck has been Professor of Mechanics of Materials at University of Cambridge Engineering Department since 1997. His research is centred on the mechanics of microstructure, ranging from failure of composites to lattice materials. He has pioneered the use of strain gradient plasticity theory to probe size effects in metals. |
|
10:30 - 11:00 | Coffee | |
11:00 - 11:45 |
Hydrogen embrittlement investigated by novel critical experiments
Among the experimental approaches to the hydrogen induced degradation, small scale testing has the capability to resolve the hydrogen interaction with microstructure and the crystal defects in the same length scale. However, small scale testing inquiries in situ examination to avoid hydrogen gradient or depletion on the testing materials. In this approach, in situ nanoindentation experiment capable of registering the onset of plasticity in a sub micro meter scale showed a reduction in dislocation nucleation energy in the presence of hydrogen. Going one step forward, in this study, we used the in situ electrochemical cantilever bending test method to probe the effect of hydrogen on the crack propagation in the micron sized notched beams. The experimantal setup is the integration of a miniaturized three electrode electrochemical cell inside a nanoindenter. This experimental method has the advantage of providing a complete overview of the plasticity and dislocations on the entire sample by post-mortem analyses. For this study Fe- 3wt% Si single and bi-crystal microcantilevers have been investigated. Mechanical behavior of the beams bent under hydrogen charging condition are compared with the air condition. The load-displacement curves reveal a continuous decrease in the flow stress for the cantilevers bent within the presence of hydrogen. Crack initiation and propagation are examined in the presence of hydrogen while the notch blunting occurs for the beams bent< in the air. Post-mortem cross-sectional EBSD analyses of the beams showed a localized plastic region for the hydrogen condition comparing with the air one. ![]() Tarlan Hajilou, Norwegian University of Science and Technology, Norway
![]() Tarlan Hajilou, Norwegian University of Science and Technology, NorwayTarlan Hajilou, is a PhD candidate at Norwegian University of Science and Technology. She received the B.Sc. degree in extractive metallurgy in 2010, and the M.Sc. in degree metallic materials selection and characterization in 2012, from Sahand University of technology in Tabriz, Iran. For her master thesis, she did research on the nanostructured, low temperature bainitic steels. She is doing her PhD, under supervision of Professor Afrooz Barnoush in the field of Hydrogen Embrittlement. |
|
11:45 - 12:30 |
Hydrogen induced stress cracking in steels – examples of failures and numerical modelling
The occurrence of cracks in offshore structures and pipelines is an environmental and safety risk that should be eliminated. Hydrogen Induced Stress Cracking (HISC) has been a challenge in the Norwegian oil & gas industry since the late 1990s. The main sources of hydrogen are cathodic protection and to some extent also hydrogen from welding. Hydrogen induced stress cracking from cathodic protection is a result of interconnected mechanisms involving electrochemistry, diffusion, metallurgy and hydrogen degradation at different length scales from the nano- to the macro-scale. Safe service requires predictive tools for assessing the structural integrity under CP conditions. For several years our group at SINTEF has worked with numerical models applying hydrogen informed cohesive zone elements to model HISC fracture as well as hydrogen-induced fracture in general. Numerical simulation of hydrogen embrittlement requires a coupled approach; on one side, the models describing hydrogen transport must account for local mechanical fields, while on the other side, the effect of hydrogen on the accelerated material damage must be implemented into the model describing crack initiation and growth. The talk will include examples of HISC fractures from the oil and gas industry as well as a review of numerical cohesive zone approaches for the prediction of hydrogen embrittlement. ![]() Dr Vigdis Olden, SINTEF Materials and Nanotechnology, Trondheim, Norway
![]() Dr Vigdis Olden, SINTEF Materials and Nanotechnology, Trondheim, NorwayDr Vigdis Olden is a senior research scientist at the research foundation SINTEF in Trondheim, Norway, where she has been employed for the last 25 years. She has a MSc in physical metallurgy and a PhD in numerical simulation of hydrogen induced fracture. |
|
12:30 - 13:30 | Lunch | |
13:45 - 14:30 |
Effects of hydrogen on fatigue crack growth in steel
In the context of the fatigue life design of components, particularly those destined for use in hydrogen refueling stations and fuel cell vehicles, it is important to understand the hydrogen-induced, fatigue crack growth (FCG) acceleration in steels. In the presentation, existing studies on the hydrogen-induced, FCG acceleration in various steels are first briefly reviewed, together with the acceleration mechanism and some of its influencing factors. The focus is then placed on the peculiar frequency dependence of the hydrogen-induced, FCG acceleration in steels. In a high-frequency regime (e.g., 10 ~ 0.1 Hz), the ratio of hydrogen-induced, FCG acceleration is seen to gradually increase with a decrease in test frequency, later reaching a peak. To justify the interpretation of the mechanism based on the hydrogen-enhanced successive fatigue crack growth (HESFCG) model, using both “internal” and “external” hydrogen, some critical experiments were performed on two types of material: Type 304 stainless steel and ductile cast iron. ![]() Professor Hisao Matsunaga, Kyushu University, Japan
![]() Professor Hisao Matsunaga, Kyushu University, JapanHisao Matsunaga received the degree of Dr. Eng. at Department of Mechanical Engineering of Kyushu University in 2002. After I worked in the same department as a Lecturer until 2005, when Matsunaga moved to Department of Mechanical Engineering of Fukuoka University as an Associate Professor. In 2012, he moved back to Kyushu University as an Associate professor. During my 15-year career in the Universities, Matsunaga has been studying metal fatigue and hydrogen embrittlement. From 2012, he concurrently belongs to the Research Center for Hydrogen industrial Use and Storage (HYDROGENIUS) in Kyushu University, and he is involved in a NEDO project aimed at the revision of domestic regulations and standards for structural materials used for hydrogen service. Matsunaga is also contributing actively to the international discussion about code and standard for hydrogen components in SAE, CSA and IEA. |
|
14:30 - 15:30 | Tea |
Chair
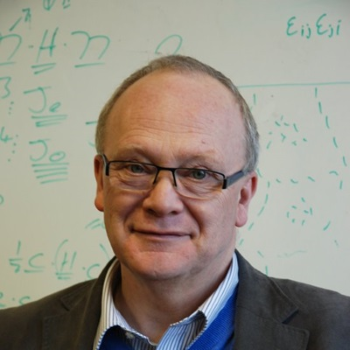
Professor Adrian Sutton FRS, Imperial College London, UK
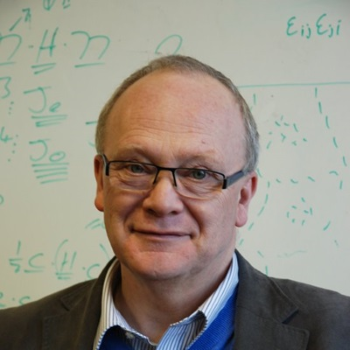
Professor Adrian Sutton FRS, Imperial College London, UK
Adrian Sutton is a professor in the Department of Physics at Imperial College London. Educated at Oxford and the University of Pennsylvania as a materials scientist he has worked in materials physics for 40 years. Since he moved to Imperial in 2005 his research has focussed on electronic excitations during irradiation damage of metals, an elastodynamic treatment of dislocations during shocks in metals, and modelling the molecular structure, plasticity and mass transport in polymers. He has had an interest in interfaces in crystalline materials throughout his research career, and with R W Balluffi published a research monograph “Interfaces in crystalline materials” in 1995, which remains the standard text on the subject. He is one of the four fellows of the Royal Society who founded in 2005 the Thomas Young Centre, the London Centre for Theory and Simulation of Materials. In 2009 he became the founding driector of the EPSRC Centre for Doctoral Training on Theory and Simulation of Materials at Imperial College London.
15:30 - 17:00 |
Panellists
![]() Professor Afrooz Barnoush, Norwegian University of Science and Technology, Norway
![]() Professor Afrooz Barnoush, Norwegian University of Science and Technology, NorwayDr Barnoush received the B.A. degree in extractive metallurgy of nonferrous alloys in 1997, and the M.Sc. degree in corrosion engineering in 1999, from Sharif University of technology in Tehran. After four years working in industry as a consultant engineer in the field of corrosion and corrosion protection he moved to Germany where he received his Ph.D. from Saarland University. The topic of his PhD thesis was “Hydrogen embrittlement revisited by in situ electrochemical nanoindentation”. After four years of research and teaching in Saarland University as a tenure track (Habiltant) he moved to NTNU, Trondheim where he become the professor of materials science. His main area of research is nano- and micro- mechanics of materials with special focus on environmental effects. ![]() Professor David Dye, Imperial College London, UK
![]() Professor David Dye, Imperial College London, UKDavid Dye is a Professor of Metallurgy in the Department of Materials at Imperial College London, UK. He mostly works on the fatigue mechanisms, micromechanics and design of titanium and nickel/cobalt superalloys, with additional interests in twinning induced plasticity steels, zirconium and in superelastic NiTi-based alloys. Primarily, he collaborates with Rolls-Royce and across the aerospace and nuclear sectors. Prior to moving to Imperial in 2003, he worked at the neutron spectroscopy facility in Chalk River, Canada. His undergraduate degree and PhD were from Cambridge University, on the weldability of nickel-base superalloys. He has received a number of awards for his work on welding of superalloys and on titanium alloys, has published over 80 journal articles and was an EPSRC Leadership Fellow, 2010-15. ![]() Professor Xavier Feaugas, Université de la Rochelle, France
![]() Professor Xavier Feaugas, Université de la Rochelle, FranceProfessor Xavier Feaugas became Research Vice President of the University of La Rochelle (ULR) in 2016. He is a Full Professor in the Department of Physic at the ULR where he has been a faculty member since 2001. He holds the position of Deputy director of LaSIE Laboratory, UMR CNRS 7356 (Laboratoire des sciences de l’ingénieur pour l’environnement) since 2012. Xavier Feaugas received his Ph.D. in Mechanics and Material with honours at University of Technology of Compiègne in 1994. Before, He had studied at UTC and graduated as a Master degree in Applied Mechanics and Materials and as a Mechanical Engineer with distinction in 1990. In 1996, He joined the Roberval UTC-CNRS laboratory as Assistant professor and developed researches on Dislocation Patterns during 1996-2001. After being promoted in 2001 to full Professor of Solid State Physics at the University of La Rochelle, he initiated researches on the area of stress corrosion cracking. Since 2001, he has been the leader of DMRS Team focus on the different interactions between metallurgical states, plasticity and surface reactivity. During 2001-2007, he was a manager of a Master of Material Science and from 2008 to 2012 he served as a director of LEMMA laboratory at ULR. ![]() Professor Hisao Matsunaga, Kyushu University, Japan
![]() Professor Hisao Matsunaga, Kyushu University, JapanHisao Matsunaga received the degree of Dr. Eng. at Department of Mechanical Engineering of Kyushu University in 2002. After I worked in the same department as a Lecturer until 2005, when Matsunaga moved to Department of Mechanical Engineering of Fukuoka University as an Associate Professor. In 2012, he moved back to Kyushu University as an Associate professor. During my 15-year career in the Universities, Matsunaga has been studying metal fatigue and hydrogen embrittlement. From 2012, he concurrently belongs to the Research Center for Hydrogen industrial Use and Storage (HYDROGENIUS) in Kyushu University, and he is involved in a NEDO project aimed at the revision of domestic regulations and standards for structural materials used for hydrogen service. Matsunaga is also contributing actively to the international discussion about code and standard for hydrogen components in SAE, CSA and IEA. ![]() Professor Barbara Shollock, University of Warwick, UK
![]() Professor Barbara Shollock, University of Warwick, UKProfessor Barbara Shollock is Academic Director of WMG and Professor within the Steels Processing research group. Professor Shollock joined WMG in 2014 from Imperial College London where she was a Senior Lecturer. She gained her undergraduate degree from Lehigh University, Pennsylvania and D.Phil from University of Oxford. She has been a TFR visiting Professor at Technical University of Lulea Sweden and held an industrial fellowship with The Royal Society. |
---|
11:45 - 12:30 |
Hydrides and zirconium - a micromechanics story
Zirconium is used as reactor fuel cladding materials in water based nuclear reactors. The oxidation of the Zr may result in both the ingress of hydrogen and the formation of hydrides. In this talk in-situ (X-ray and SEM) based micropillar experiments at both room temperature and ~reactor temperature to probe the behaviour Zr/Zr-hydrides at the micrometer lengthscale will be presented. ![]() Dr Ben Britton, Imperial College London, UK
![]() Dr Ben Britton, Imperial College London, UKDr Britton is a RAEng Research Fellow, Deputy Director of the Centre for Nuclear Engineering, Director of the Advanced Nuclear Engineering MSc and Lecturer in Materials. His research group focus their efforts on understanding materials used in high-value high-risk applications, such as aerospace, oil & gas, and nuclear power. They utilise a mixture of experiment and simulation to probe and understand the behaviour of materials at the micrometer lengthscale. |
|
---|---|---|
12:30 - 13:30 | Lunch | |
13:30 - 14:15 |
Hydrogen effects and hydride formation in Zr and Ti alloys
In this contribution, a survey was proposed of the possible implications of hydrogen on mechanical behaviour of Zr and Ti alloys with emphasis on the mechanisms of plasticity and strain hardening. Recent advances on the impact of oxygen and hydrogen on the activation volume show that oxygen content hinders the creep and that hydrogen partially screens this effect. Both aspects are discussed in term of looking-unlocking model of the screw dislocation mobility in prismatic slip. Additionally possible extension of this behaviour is suggested for the behaviour is suggested for the <c+a> pyramidal slip. The low hydrogen solubility leads in many cases to hydride precipitation. The nature of these phases depends the hydrogen content and can show crystallographic orientation relationships with the hexagonal compact structure of the alloys. Some advances on the thermal stability of these phases are illustrated and discussed in relation with the deepening of the misfit dislocations. Under tension loading, it is shown that hydrides enhance the hardening process in relation with internal stress due to strain incompatibilities between Zr and Ti matrix and hydride phases. Different plastic yielding processes of hydride were identified, which progressively reduce these strain incompatibilities. ![]() Professor Xavier Feaugas, Université de la Rochelle, France
![]() Professor Xavier Feaugas, Université de la Rochelle, FranceProfessor Xavier Feaugas became Research Vice President of the University of La Rochelle (ULR) in 2016. He is a Full Professor in the Department of Physic at the ULR where he has been a faculty member since 2001. He holds the position of Deputy director of LaSIE Laboratory, UMR CNRS 7356 (Laboratoire des sciences de l’ingénieur pour l’environnement) since 2012. Xavier Feaugas received his Ph.D. in Mechanics and Material with honours at University of Technology of Compiègne in 1994. Before, He had studied at UTC and graduated as a Master degree in Applied Mechanics and Materials and as a Mechanical Engineer with distinction in 1990. In 1996, He joined the Roberval UTC-CNRS laboratory as Assistant professor and developed researches on Dislocation Patterns during 1996-2001. After being promoted in 2001 to full Professor of Solid State Physics at the University of La Rochelle, he initiated researches on the area of stress corrosion cracking. Since 2001, he has been the leader of DMRS Team focus on the different interactions between metallurgical states, plasticity and surface reactivity. During 2001-2007, he was a manager of a Master of Material Science and from 2008 to 2012 he served as a director of LEMMA laboratory at ULR. |
|
14:15 - 15:00 |
The role of hydrogen in stress corrosion cracking – a titanium alloy case study
Ti6246 is a high strength heavily beta stabilised titanium alloy. It finds widespread use in the aerospace industry for critical rotating components, and in the appropriate environment may exhibit stress corrosion cracking. This presentation details a particular ‘hot salt’ stress corrosion mechanism that has unusual consequences for the certification and application space for titanium alloys. The utilisation of unusual combinations of advanced experimental techniques will be detailed in the context of the more traditional failure investigation / fractographic approach. The role of hydrogen in crack tip deformation will be reviewed in the context of the high temperature and high stress experienced in this case. ![]() Dr Tamara Chapman, Rolls-Royce plc, UK
![]() Dr Tamara Chapman, Rolls-Royce plc, UKTamara has been working in the Materials, Chemistry and Corrosion department at Rolls-Royce plc since July 2016. Tamara joined Rolls-Royce Nuclear from Frazer-Nash Consultancy where she was an engineer in the Materials Performance Group. She gained her undergraduate degree in Mechanical and Materials Engineering from the University of Birmingham and PhD from Imperial College London. Tamara’s PhD was closely linked to the aerospace gas turbine industry and focussed on the hot salt stress corrosion cracking and hydrogen embrittlement mechanisms within alpha-beta titanium alloys. |
|
15:00 - 15:30 | Tea | |
15:30 - 16:15 |
Hydrogen in titanium and zirconium – an industrial perspective
Titanium has found widespread use in demanding applications dominated by the aerospace industry. Its strength to weight ratio, and critically, corrosion resistance make it well suited to highly stressed rotating components. Zirconium has more niche but no less critical application where its low neutron capture cross section and good corrosion resistance in hot water and steam make it well suited to reactor core use, including fuel cladding and structural applications. Hydrogen control during manufacture and subsequent in-service behaviour for titanium and zirconium alloys as a function of hydrogen content will be reviewed. This will include the potential for hydrogen ‘pick up’ in service for nuclear and aerospace sectors. Empirically derived manufacturing methods and design / certification criteria will be detailed for pertinent material types and load regimes. Much of our understanding about hydrogen in titanium and zirconium is inferred from macroscopic testing. Predictive capability for failure and the potentially subtle interplay between alloy chemistry, microstructure and hydrogen (location, mobility and degradation mechanisms) is therefore limited. This paper will also review the current mechanistic understanding relating to hydrogen in high purity metals along with important alloy systems. The role of beta phase in hydrogen ‘pick-up’, trapping and transport will be discussed along with possible crack initiation mechanisms In addition, the scope for progress in this area over the next decade with respect to both developments in experimental techniques and physics based modelling capability will be discussed. ![]() Professor Dave Rugg FREng, Senior Fellow, Rolls-Royce plc, UK
![]() Professor Dave Rugg FREng, Senior Fellow, Rolls-Royce plc, UKDave is a metallurgist who started his career with a PhD on Magnesium alloys around 30 years ago. After this he spent seven years at IMI Titanium in the R+D group conducting research on alloy and process development. For the last two decades Dave has worked at Rolls-Royce in a variety of roles including long term, extensive and highly stimulating interaction with academia with an emphasis on titanium and zirconium research. His interests include cutting edge experimental techniques through to physics based modelling in order to address industrial problems. Dave spent three very happy years as a Royal Society Industrial Fellow, mainly based at Oxford. His current role is Rolls-Royce Senior Fellow for materials which spans all materials and business sectors covering the full life product cycle. |
Chair
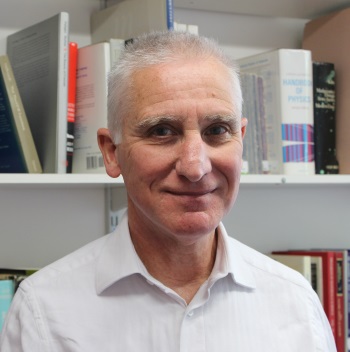
Professor Anthony Paxton, Kings' College London, UK
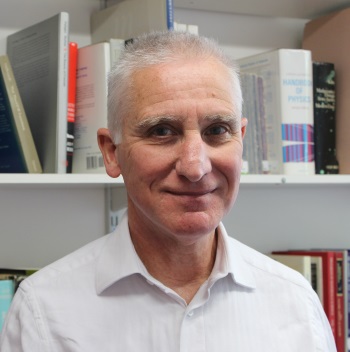
Professor Anthony Paxton, Kings' College London, UK
Tony Paxton trained as a metallurgist at Sheffield and Oxford; was employed as a physicist at Max-Planck-Institut für Festkörperforschung and at SRI International. He returned to Oxford as an SERC Advanced Fellow and in 1995 took up a Lectureship at Queen’s University Belfast, later taking a Chair Theory and Modelling in Condensed Matter. In 2013 he moved to King’s College to become Professor of Computational Materials Science. He is a Visiting Professor in the Faculty of Engineering at Imperial College. He is interested in structure-property relations in metals, working with colleagues at Sheffield, Oxford, Cambridge and Imperial College, and at Magnesium Elektron, Rolls-Royce, SKF and ThyssenKrupp Steel Europe. He has interests in ice, water and electrochemical processes.
16:15 - 17:00 |
Panellists
![]() Yun Deng, Norwegian University of Science and Technology, Norway
![]() Yun Deng, Norwegian University of Science and Technology, NorwayYun Deng is a PhD student in Norwegian University of Science and Technology (NTNU), Trondheim, Norway. She got her bachelor degree in Materials Physics in University of Science and Technology Beijing, China in 2011. After that, she went to Germany and finished her Master study in Department of Physical Metallurgy and Metal Physics in RWTH Aachen University in 2014. During the meantime, she worked one year in the Department of Microstructure Physics and Alloy in Max-Planck institute for iron research on topic of high entropy alloy in Düsseldorf. Now she works as a PhD student in NTNU with Prof. Afrooz Barnoush focusing on the research of Hydrogen Embrittlement. ![]() Dr Tilmann Hickel, Max-Planck-Institut für Eisenforschung GmbH, Germany
![]() Dr Tilmann Hickel, Max-Planck-Institut für Eisenforschung GmbH, GermanyTilmann Hickel studied physics at Humboldt University Berlin, Germany, and Loughborough University, England, and finished his PhD in 2005 on many-body theories for magnetic materials. He afterwards joined the Max-Planck-Institut für Eisenforschung GmbH, where he became in 2006 head of the group “Computational phase studies” within the department “Computational Materials Design”. His group focuses on the ab initio based simulation of materials properties and phase stabilities at finite temperatures, with a particular focus on steels. ![]() Professor Mary Ryan FREng, Imperial College London, UK
![]() Professor Mary Ryan FREng, Imperial College London, UKMary joined Imperial College in 1998 having spent three years at Brookhaven National Laboratory in the US, first as a post-doctoral researcher and then as staff scientist in the Materials Division. Her doctoral work at the University of Manchester was on the use of in-situ ECSTM to study the formation of ultra-thin surface oxides on base metals, showing for the first time that these surfaces are crystalline phases. At Brookhaven she developed the use of in-situ techniques in electrochemical systems, this time with synchrotron radiation-based techniques. Her current research is in the area of applied electrochemistry and corrosion, with a focus on deposition of nanostructures and the study of self-forming nanocrystalline oxides; as well as fundamental work on degradation and stability of metal systems. She is a Fellow of the Institute of Materials Mining and Minerals (member of the Corrosion Committee and Corrosion Network 2015-) and a member of the International Society of Electrochemistry (Materials Division Chair 2013-2015). ![]() Jon Saltmarsh, Department for Business, Energy and Industrial Strategy, UK
![]() Jon Saltmarsh, Department for Business, Energy and Industrial Strategy, UKJon Saltmarsh is Head of Technical Energy Analysis within the Department for Business, Energy and Industrial Strategy. His role involves gathering evidence and providing technical advice to underpin the UK Government’s policies on reducing demand for energy and providing cost effective carbon reduction in the built environment. This covers both energy efficiency and the use of locally generated, low carbon energy sources, particularly for heat. Specific areas of interest include: understanding energy use in buildings; smart technologies to manage demand and improve the consumer experience; heat pumps; hydrogen for heat; novel technologies and whole system modelling. Prior to joining DECC, he ran a number of cutting edge technology development programmes. These provided low carbon alternatives to what were traditionally highly energy intensive activities. They included the world record breaking Zephyr, solar powered aircraft, designed to provide a low cost substitute for satellites; and sophisticated, networked simulators to replace aircraft flying hours with ground based synthetic training. Jon holds a degree in Engineering from St John’s College Cambridge and an MBA from Cranfield University. |
---|