Sustainable metals: science and systems
Scientific discussion meeting organised by Professor Julian M Allwood FREng and Professor Dierk Raabe.
Discussions on global warming and metal production suffer from a disconnect between environmental systems analysis which is technologically vague and materials innovations that cannot scale sufficiently to have meaningful impact. The meeting aimed to nucleate a new research community focused on scalable solutions that allow the global metals system to function with zero emissions by 2050.
The schedule of talks and speaker biographies are available below. Speaker abstracts are also available below. Meeting papers will be published in a future issue of Philosophical Transactions of the Royal Society A.
Attending this event
This event has taken place.
Enquiries: contact the Scientific Programmes team
Journal
Organisers
Schedule
Chair
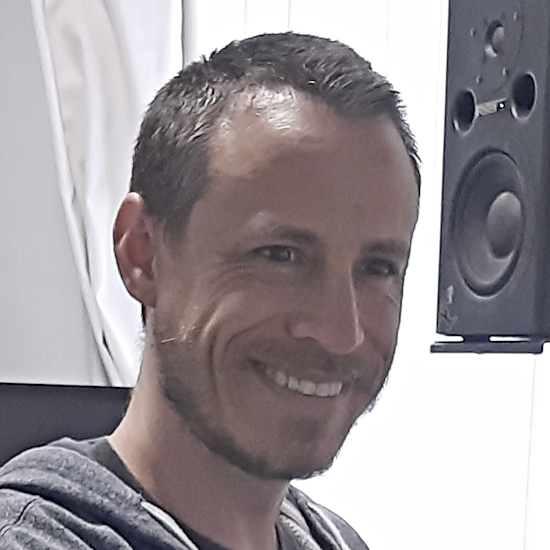
Dr Alec Davis, University of Manchester, UK
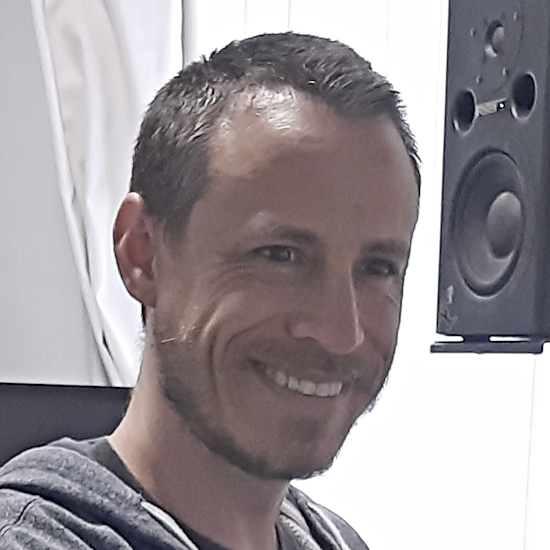
Dr Alec Davis, University of Manchester, UK
Dr Alec Davis is a lecturer in metallurgy and materials characterisation at the University of Manchester, UK. His research is primarily focussed on titanium, magnesium, and nickel-based superalloy metallurgy and additive manufacturing, through the use of large-scale, high-throughput, in-situ, and 3D electron microscopy characterisation techniques, coupled with plasticity and thermodynamic modelling.
09:00-09:05 |
Introduction
|
---|---|
09:05-09:30 |
Decarbonising the global steel industry in a resource-constrained future – a systems perspective
Decarbonising the global steel industry hinges on three key limited resources: geological carbon storage, zero emission electricity, and end-of-life scrap. Existing systems analysis calls for an accelerated expansion of the supply of these resources to meet the assumed ever-increasing steel demand. In this talk, Dr Watari proposes a different view on how to decarbonise the global steel industry, based on the precautionary principle that resource supply can only expand in line with historical trends and actual construction plans. The analysis shows that global steel production cannot grow any further within a carbon budget and conservative resource supply, resulting in a ~60% shortfall against 2050 demand. The trajectory involves the phasing out of blast furnace production, while recycling-based production will double by 2050, along with modest growth in hydrogen-based production. These findings highlight critical yet often overlooked challenges: (1) reducing demand while providing essential services, (2) producing high-grade steel through upcycling scrap, and (3) ensuring an equitable distribution of recycling-based production across the globe. These perspectives contrast with that of the current agenda, which almost exclusively emphasises the need to invest in new production technologies and resource supplies. Given the slow and staggering progress in decarbonising the steel industry, this talk aims to offer a complementary perspective for a more balanced debate in policymaking and industrial strategy. ![]() Dr Takuma Watari, National Institute for Environmental Studies, Japan
![]() Dr Takuma Watari, National Institute for Environmental Studies, JapanTakuma is a tenure-track researcher at the National Institute for Environmental Studies, Japan, and a JSPS Research Fellow at Leiden University, the Netherlands. Previously, he worked at the University of Cambridge, UK, and the University of Technology Sydney, Australia. His primary research interests include industrial decarbonisation, responsible supply of critical materials, and international equity in resource use. His work combines traditional engineering principles with systems analysis, and has been published in leading multidisciplinary scientific journals. He currently leads several research projects on sustainable materials use and works closely with government and industry to apply a systems perspective to decision-making. |
09:30-09:45 |
Discussion
|
09:45-10:15 |
A key feedback loop: electrifying metals production to electrify society
There is a division in the literature regarding the future availability of low or zero-carbon energy, driven partially by differing estimates of the resource requirements for energy infrastructure. Dr Daehn starts with an investigation into the resource requirements for a net-zero energy system, with a focus on bulk materials and energy inputs. She argues that the infrastructure requirements are largely achievable, and the metals industry can play a key reinforcing role in the transition by adapting to the increasing supply of renewable electricity. Specifically, direct electrolysis can extract metal from ore much closer to the thermodynamic limit, to make efficient use of low-C electricity while decoupling extraction from GHG emissions. The unique features and recent advancements of emerging technologies for iron extraction, molten oxide electrolysis (MOE) and molten sulphide electrolysis (MSE), are described and modelled in this evolving system. Though long time scales are required, electrification enables elegant separations of ore and scrap feedstocks, and provides a pathway to build out abundant renewable energy while continually reducing environmental impacts. ![]() Dr Katrin Daehn, Massachusetts Institute of Technology, USA
![]() Dr Katrin Daehn, Massachusetts Institute of Technology, USAKatie grew up in Columbus, Ohio and earned her BS in Materials Science and Engineering at the Ohio State University in 2015. She then went onto a PhD in Engineering at the University of Cambridge (completed in 2019) as a Cambridge Trust scholar, working with Professor Julian Allwood on end-of-life steel recycling. She is now a postdoctoral researcher in the MIT Climate and Sustainability Consortium helping to develop cross-sector strategies to decarbonize the global economy. Achievements she is particularly proud of include receiving the Goldwater scholarship, authoring the Top Policy paper in Environmental Science and Technology (2017), and working with a team to extract copper and iron from ore using only electricity in Professor Antoine Allanore’s lab. She is a third-generation metallurgist and wants to spend her career improving the management of Earth’s resources. |
10:15-10:30 |
Discussion
|
10:30-11:00 |
Break
|
11:00-11:30 |
Sustainable extraction of non-ferrous metals
The recycling of metals makes a significant contribution to resource and energy efficiency. In this context, however, the entire metal cycle must be considered, including primary metallurgy as well as zero-waste concepts and material design. In addition, today's process technologies are not yet optimized in terms of process engineering and economics with regard to the variety of input materials, scrap and metal-containing residual materials. In particular, the element distributions in the individual phases are not always known. In the case of base metals such as aluminium, magnesium and titanium, the variety of alloys poses a major challenge in the field of recycling technologies, as for the most part no refining options exist. However, the variety of elements, coating and bonding systems in end-of-life products, which are a necessity due to the required functionality, very often means that only a few metals are recovered. Comprehensive multi-metal recycling does not currently exist. This requires research and development in the area of process optimization and the recycling of by-products generated during the processes. Using examples in the field of light and heavy metals, the challenges and possible solutions will be explained and future research priorities discussed. The targeted networking of collection, processing and material recycling as well as the interaction with primary metallurgy are the focus of the considerations. Dipl-Ing Dr mont Eva Gerold, University of Leoben, Austria
Dipl-Ing Dr mont Eva Gerold, University of Leoben, Austria |
11:30-11:45 |
Discussion
|
11:45-12:15 |
Recycling innovations to utilise waste into sustainable green metal manufacturing
Most of the electronic waste, spent batteries and polymer-metal laminated flexible packaging waste are the problematic solid waste streams around the world today which are destined to be stockpiled/landfilled or transported overseas in developing countries. The rapid uptake of technology and energy storage systems with the advent of new designs at regular intervals and intense marketing in the electronics sector and other consumer goods is causing the early obsolescence of many products. However, these waste sources are embedded with valuable metals such as copper, tin, aluminium, cobalt, nickel, lithium, etc. Due to the ongoing demands for valuable metals for different applications, global industrial and manufacturing supply chains must embrace strategies in which conventional resources could be replaced by resources extracted from waste that are currently lost to landfills and other uncertain futures. Selective thermal transformation of waste, in small-scale MICROfactoriesTM, can enable decentralised processing of waste resources by businesses large and small, in modular systems, into valuable ‘Green Metals’ for feedstock. This will create stocks of value-added sustainable metal alloys which could become part of supply chains for manufacturing, support the manufacturing and energy industry, and protect the environment. ![]() Dr Rumana Hossain, Centre for Sustainable Materials Research & Technology, SMaRT@UNSW, University of New South Wales, Australia
![]() Dr Rumana Hossain, Centre for Sustainable Materials Research & Technology, SMaRT@UNSW, University of New South Wales, AustraliaRecipient of an Australian Postgraduate award, Dr Rumana Hossain is a material scientist and engineer, an expert on innovative solutions for waste challenges. Her research experience of working with industries and in research commercialisation promotes a culture of innovation to particularly bridge the gap between pure and applied research to transform waste into valuable materials for sustainable manufacturing and environment. Her research activities at SMaRT@UNSW Sydney includes leading industrial projects for waste recycling solutions, publishing in high-impact journals, and building strong networks across diverse industries, communities, national and international research institutions. |
12:15-12:30 |
Discussion
|
Chair
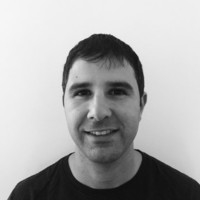
Dr Enzo Liotti, University of Oxford, UK
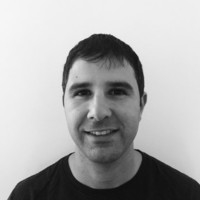
Dr Enzo Liotti, University of Oxford, UK
Dr Enzo Liotti is a Departmental Lecturer at the Department of Materials, University of Oxford, United Kingdom. His research focus on using and developing X-ray synchrotron techniques for the investigation of fundamental dynamic phenomena in metal processing and material science, with particular interest in solidification of metal alloys. He obtained his BSc and MSc in Material Engineering from the Politecnico di Milano (Italy) and gained a PhD in Materials science in 2011 from the University of Loughborough (UK), with a project on the characterization of a nano-quasicrystalline containing Al alloy with high temperature mechanical properties. From 2011 to 2019 he was a PDRA at the department of Materials, University of Oxford, working on in-situ imaging of solidification within professor P S Grant’s Processing of Advanced Materials Group.
13:30-14:00 |
On the combustion and regeneration of sustainable Fe-based fuel
An urgent decarbonization of the energy sector is required to combat global warming, as this sector accounts for more than 70% global CO2 emissions due to the use of fossil fuel. Sustainable energy storage technology is a key to this transition due to the spatiotemporal intermittence of sustainable energy production based on solar, winder, hydropower, and geothermal energies, etc. Recently, metal fuels were proposed as high energy dense and sustainable energy carriers. In particular, iron powder is very promising due to its relatively low-cost, safety, abundance, and facilitated retrofit of the power plants. The stored energy is released during the combustion of the metallic powder. The product of the combustion, iron oxide powder, is then regenerated by hydrogen-based solid-state direct reduction. A net CO2-free emission closed cycle of energy storage is obtained, when the hydrogen is produced using renewable energy sources. While the first studies on pure iron combustion and regeneration are very promising, the influence of eventual impurities inside the Fe-based powders on the combustion and reduction processes has never been studied. Yet, increasing the tolerated amount of impurities in the iron powder will increase its economic competitiveness, as well as potentially improve the combustion/regeneration processes. During this presentation, Dr Choisez will present an overview of the current understanding of the combustion and hydrogen-based direct reduction of pure iron powders, as well as the expected influence of several impurities on the combustion and regeneration of Fe-based sustainable fuel. ![]() Dr Laurine Choisez, Université Catholique de Louvain, Belgium
![]() Dr Laurine Choisez, Université Catholique de Louvain, BelgiumDr-Ing Laurine Choisez is currently working at the Université Catholique de Louvain, Belgium, as chargé de recherche FNRS on the topic of sustainable iron powder fuel. She started working on iron fuel during her post-doc at the Max-Planck Institute for Iron Research in 2021. She received her PhD in 2021 at the Université Catholique de Louvain, Belgium, where she also graduated as a materials science engineer in 2016. She also had the opportunity of studying martensitic transformation in ceramic shape memory alloys in 2015 at MIT. Her current research interests lie from metal fuel, iron combustion and hydrogen-based reduction of iron ores to beta-metastable Ti alloys, damage mechanisms and defect tolerant materials for 3D printing. Dr Choisez received the Chair Lhoist Berghmans grant in 2015, the FNRS grant for doctoral researcher in 2016 and the FNRS grant for postdoc research, received in 2022. |
---|---|
14:00-14:15 |
Discussion
|
14:15-14:45 |
Residues from nonferrous metallurgical industry – a potential future supply source for scarce metals
At various non-ferrous metal production sites, the production of the main raw metals requires the removal of impurities associated and introduced with the ore concentrates. This extractive metallurgy produces slags, dusts, sludges, or precipitation residues as a byproduct. The current common practice of disposing of these residues not only generates considerable landfill volumes, but also results in the loss of significant quantities of scarce and valuable elements contained in these materials, including nickel, silver, cobalt, indium, and others. The growing awareness of the need for these high-tech metals in the technologies required for the energy transition, climate protection, the electrification of mobility and also for the independence of metal production in Europe, is bringing these materials, which have been ignored for years, back into the focus of science. Against this background, the presentation will attempt to discuss the material flows of the base metals industry, such as zinc, lead, copper, or aluminium, the genesis of selected generated residues and their possible contained scarce valuable metals. Using an example from nickel- and zinc-metallurgy, furthermore the challenges and complexity during characterization of these materials and the associated necessary holistic approach during the fundamental research in the area of process development to find scalable solutions will be discussed. ![]() PD Assistant Professor Stefan Steinlechner, Christian Doppler Laboratory, Montanuniversität Leoben, Austria
![]() PD Assistant Professor Stefan Steinlechner, Christian Doppler Laboratory, Montanuniversität Leoben, AustriaStefan Steinlechner studied metallurgy at the Montanuniversität Leoben in Austria and defended his PhD in the year 2013. Since then, he has been working as a postdoctoral researcher at the Chair of Nonferrous Metallurgy. From 2014 to 2018 Stefan Steinlechner was responsible for a Research-Studio-Austria focusing on energy and resource efficiency in metal recycling from industrial residues. In 2018 he was appointed the venia docendi for the metallurgy of nonferrous metals and since 2020 he has been Head of the "Christian Doppler Laboratory for the selective recovery of minor metals using innovative process concepts". |
14:45-15:00 |
Discussion
|
15:00-15:30 |
Break
|
15:30-16:00 |
The role of co-product valorisation and grass-roots cooperation in sustainable metals systems
As metals are the cornerstone of the sustainable development of our society and have an important contribution to the clean energy transition, a sustainable metals industry is a critical necessity for our future sustainable society. Among the key enablers for sustainable metals systems are stable and sufficient access to resources, climate change neutral or even positive processes, an involved community with engaged professionals and a long-term vision and strategy set by stakeholders, policymakers and public authorities. The establishment of multi-stakeholders partnerships and network collaborations is crucial for this transition to sustainable metals systems. A recent initiative is the launch of Flanders Metals Valley in 2021, a bottom-up initiative in which its members, consisting of companies, universities and knowledge centres, collaborate to create a climate-neutral circular metals industry and to be a stellar example of industrial symbiosis. Within the vision of Flanders Metals Valley, by acting as a network, metals circularity can be improved by jointly developing solutions for particular co-products. The creation of these solutions relies on the close collaboration between industry and knowledge partners to enable ground-breaking innovative research which is supplying answers to the challenges faced by industry today. Dr Malfliet will discuss the role and vision of Flanders Metals Valley in creating a climate-neutral circular metals industry and illustrate the industry-university collaboration for the research in the field of the valorisation of co-products. ![]() Dr Annelies Malfliet, KU Leuven, Belgium
![]() Dr Annelies Malfliet, KU Leuven, BelgiumDr Ir Annelies Malfliet is a research expert at the Department of Materials Engineering at the KU Leuven, where she is affiliated to the group of High Temperature Processes and Industrial Ecology. Her expertise lies in the field of ferrous and non-ferrous metallurgy, in particular on high temperature metal processing, residue valorisation, metal recovery and vessel integrity. Annelies Malfliet is coordinator of the Centre for High Temperature Processes and Sustainable Materials Management, which is a close collaboration between the research group and leading metallurgical companies in Flanders. She is also member of the steering group of Flanders Metals Valley (FMV), a network of metallurgical companies, research institutes and universities in and around Flanders to stimulate enthusing education and groundbreaking research in the field of climate-neutral and circular metallurgy. She is author of 73 peer-reviewed publications and 7 book chapters. |
16:00-16:15 |
Discussion
|
16:15-17:00 |
Poster flash talks
|
17:00-18:15 |
Poster session
|
Chair
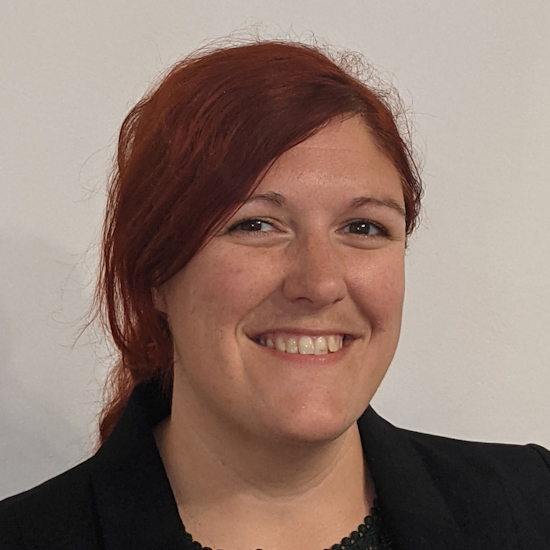
Dr Katie McFall, University College London, UK
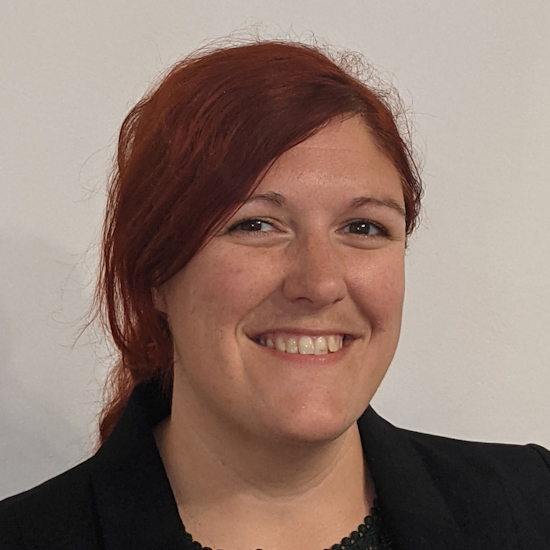
Dr Katie McFall, University College London, UK
Dr Katie McFall is a Lecturer in Economic Geology at University College London, where she researches and teaches how to find more sustainable supplies of the resources needed for the energy transition. After obtaining her PhD on critical metals in copper deposits from the University of Southampton in 2017, Katie worked as a postdoctoral researcher at Cardiff University for 5 years, researching the potential of by-products in a range of mineral deposit types, and the formation mechanisms of critical metal bearing ore deposits. Katie works extensively with the mining industry, with successful research partnerships in the fields of mineral exploration, processing mineralogy, mine waste and ESG. She is the Director of the UCL Earth Resources Centre, and is Chair of the Mineral Deposit Studies Group, an affiliated group of the Geological Society of London.
09:00-09:30 |
Reuse, remanufacturing and recycling in the steel sector
The global steel sector is undergoing a transition from being a major CO2 emitter to a more sustainable circular material approach. To achieve the ambitious aims greater reuse, remanufacturing and recycling of steel products is required alongside the use of green energy, such as hydrogen, to produce iron. Reuse and remanufacturing require knowledge of a components remaining life at the end of product life and options for disassembly and repurposing. Increased recycling of obsolete scrap has implications on composition control with increases in residual elements, such as Cu, Sn, Cr, Ni inevitable. This paper discusses the opportunities for the steel sector to move to (near) net zero CO2 production through the combined strategies of reuse, remanufacturing, recycling and changes to the primary steelmaking approaches, using the UK as an example based on the current state of the sector and potential future options. Case studies will be presented on the assessment of component service loading and remaining life at the end of product life that supports decisions for reuse and remanufacturing, focussing on steel intensive applications in the transport sector. The impact of recycling on the residual element content in steel will be discussed along with examples of how these elements can affect the microstructural development during steel processing. ![]() Professor Claire Davis, WMG, University of Warwick, UK
![]() Professor Claire Davis, WMG, University of Warwick, UKProfessor Claire Davis holds a RAEng / Tata Steel Chair in Low Energy Steel Processing and leads the Advanced Steel Research Centre at WMG, University of Warwick. Claire’s research interests are the links between steel microstructure-processing- properties and she works in close collaboration with the steel industry. She is a member of the EPSRC funded Manufacturing the Future Hub SUSTAIN, which aims to deliver cutting edge science and the engineering research required to create carbon neutral, resource-efficient UK steel supply chains, and the UKRI funded interdisciplinary centre CircularMetal working towards full metal circularity with a focus on steel and aluminium. |
---|---|
09:30-09:45 |
Discussion
|
09:45-10:15 |
Mining of primary raw materials as the critical foundation of ‘sustainable’ metals: a wicked problem for technology innovation clusters
A transition to a more sustainable human-nature system is inextricably linked to raw materials production, because the most voracious and dominant consumers in society operate within a paradigm of economic growth. In order to maintain or increase consumption while limiting the impacts of climate change, technology innovation clusters are emerging that require more, not less, mining - for a widening array of materials at rapidly increasing volumes and increasing energy demand. A wicked problem therefore arises whereby there is no point in human history, or prehistory, at which global power-bases have had so little opportunity to decrease dependence on mined raw materials without threatening the fabric of their societies. Dr Moore interrogates the issue of what constitutes a sustainable metal from a triple perspective: (1) the characteristics of ore deposits and the primary extractive operations that supply metal feedstocks; (2) the impediments for complex and interacting supply chains to maintain critical (and other) metals in use; (3) the lack of transparency in supply chains that mask unsustainable practices in raw materials production. She examines existing and emerging structures for resource management, to articulate the limits to the circular economy and what constitutes a meaningful systemic structure for primary production by responsible mining. As a consequence, she calls for the inclusion of a standardised statement of the ‘natural capital’ embodied in R&D for technological materials, as a means to create transparency about what constitutes a sustainable metal. ![]() Dr Kathryn Moore, Cambourne School of Mines, University of Exeter, UK
![]() Dr Kathryn Moore, Cambourne School of Mines, University of Exeter, UKKate Moore is a geologist and specialist in Critical and Green Technology Metals at the Camborne School of Mines, University of Exeter (UK). Her 30 years of interdisciplinary research experience include: metal ore-forming geological systems; the scales of mining and diffusion of innovation to improve security of supply of metals; technical and societal innovations towards sustainable futures; and knowledge-sharing in the circular economy. She was a finalist for a European Commission (Futurium) Innovation Radar Prize for Women-led Innovation in 2019 and a Royal Cornwall Polytechnic Society medallist for excellence in science in 2023. |
10:15-10:30 |
Discussion
|
10:30-11:00 |
Break
|
11:00-11:30 |
Artificial intelligence methods in sustainable metallurgy
Artificial intelligence has attracted lots of attention in the field of sustainable metallurgy in recent years. It significantly increases the efficiency and productivity of the new alloy design and process optimization to improve the sustainability and circularity of steels. The primary objective of this work is to leverage the intricate interplay between microstructure and material properties, to design steels with superior mechanical and functional properties based on the chemical composition of steel scrap. Therefore, the authors developed a framework to extract microstructural features of steels by employing a convolutional neural network-based image segmentation strategy. The database includes a wide variety of elements that affect the microstructural evolution and properties of steels. This investigation goes beyond traditional approaches by including interpretable machine learning technologies to extract composition-processing-microstructure-property relationships. Such a strategy not only simplifies the selection of the desirable compositions for specific properties, but also enables the customization of microstructures to design versatile steels based on steel-scrap chemistry. This study elevates the realm of secondary steelmaking, showcasing the potential of interpretable machine learning in sustainable metallurgy. ![]() Dr Ziyuan Rao, Max-Planck-Institut für Eisenforschung GmbH, Germany
![]() Dr Ziyuan Rao, Max-Planck-Institut für Eisenforschung GmbH, GermanyDr Ziyuan Rao is the research group leader of the group ‘Artificial Intelligence for Materials Science’ at the Max Planck Institute for Iron Research (MPIE). He earned his MS in Materials Science and Engineering from the University of Science and Technology Beijing, China. After that, he pursued his PhD studies at MPIE under the guidance of Professor Dierk Raabe. In 2021, he successfully obtained his PhD degree from RWTH Aachen University, Germany, and subsequently continued as a post-doctoral fellow at MPIE. He was appointed as a research group leader at MPIE starting in 2023. His research centres on applying artificial intelligence to materials science, encompassing alloy design, experimental data analysis, text data mining, and interpretable artificial intelligence techniques. |
11:30-11:45 |
Discussion
|
11:45-12:15 |
Crystallization process design for control of metal salt purity, size and morphology
Crystallization and precipitation of metal salts are important unit operations in metal production both from primary and secondary raw materials. Precipitation is often applied to produce concentrates or remove impurities and evaporative and cooling crystallization are widely applied to obtain high purity end-products. The crystal morphology, size, and size distribution impact the filtration, washing and drying of the solid product, which in turn has an impact of the product purity and energy consumption. Furthermore, these product characteristics can also impact downstream re-dissolution or thermal treatment steps. The product characteristics concerning morphology, crystal size and size distribution and purity can all be influenced by controlling the process conditions. By careful design of laboratory experiments key data and knowledge of relevance for upscaling of industrial crystallization of metal salts can be acquired and applied and lead to the development of more sustainable, resource efficient and energy saving processes. ![]() Professor Kerstin Forsberg, KTH Royal Institute of Technology, Sweden
![]() Professor Kerstin Forsberg, KTH Royal Institute of Technology, SwedenKerstin Forsberg is Professor of Chemical Engineering and Head of the Division for Resource Recovery at KTH Royal Institute of Technology in Stockholm, Sweden. Her research is focused on separation processes, with a specialization in crystallization and precipitation of metal salts. She often applies this knowledge to develop sustainable processes for recovery of resources from waste. She is chair of the Hydrometallurgy and Electrometallurgy Committee at The Minerals, Metals & Materials Society TMS and member of the scientific committee for the International Workshop on Industrial Crystallization BIWIC. Furthermore, she promotes multidisciplinary collaboration as deputy director of the platform for industrial transformation at KTH. |
12:15-12:30 |
Discussion
|
Chair
Dr Stella Pedrazzini, Imperial College London, UK
Dr Stella Pedrazzini, Imperial College London, UK
13:30-14:00 |
Design strategies for lower impact construction
Structural design practice is highly inefficient from a material use perspective. This comes from the structure of the design process, with decisions made at the early stages when their impact cannot be properly assessed. To then reach embodied carbon targets, the structural designers then need access to low-carbon materials, but these are in short supply, leading to increased costs without actual reductions in the embodied CO2. Here, Dr Dunant lays out the critical decisions and their impact, and show how materials can be obtained to reduce the overall carbon impact of construction. In particular, he will describe the impact of spans, and foundation design, and show how project-adapted material choices are better for the environment than one-size-fits all approaches attempting to access the same limited pool of lower-carbon resources. ![]() Dr Cyrille Dunant, University of Cambridge, UK
![]() Dr Cyrille Dunant, University of Cambridge, UKAfter a masters in mechanical engineering and a PhD in material science looking at concrete durability, he has since moving to Cambridge looked at how materials could be better used in the built environment. He has studied barriers to steel reuse and the role of risk in supply chain reconfiguration. He has developed PANDA, a structural scheme design tool, now distributed by a spin-off company, which allows early-stage interventions in structural design to save both cost and carbon. Recently, he has developed a novel way of recycling cement electrically as a co-product of steel recycling, possibly opening the way to the first scalable route for zero-emissions Portland cement production. |
---|---|
14:00-14:15 |
Discussion
|
14:15-14:45 |
Fossil-free ironmaking, recycling oriented alloys design, lean and impurity-tolerant alloys
More than 1.9 billion tons of steel are produced this year, making it the most important alloy in terms of volume, economic leverage and environmental impact. While steel is a sustainability enabler, through lightweight car parts, rail tracks, wind farms and magnets, its primary production is not. Iron is reduced from oxidic ores using fossil carbon-based reductants. This produces about 2t CO2/t of steel, standing for >30% of the global CO2 emissions in manufacturing. These emissions can be reduced when replacing carbon by hydrogen or its carriers as reductants, by the use of higher scrap fractions and by the electrification of oxide reduction. The lecture presents some recent progress in understanding the key mechanisms of hydrogen-based solid-state direct reduction and hydrogen-based plasma smelting reduction of iron ores. The kinetics of the reactions strongly depend on mass transport kinetics, nucleation during the multiple phase transformations, the oxide’s chemistry and microstructure, and on damage and fracture associated with the phase transformation and mass transport phenomena occurring during reduction. Understanding these effects is key to make hydrogen-based reduction of iron ores commercially viable, enabling massive CO2 reductions in this sector. In summary the key questions addressed in the lecture are: (a) How to make green steel by direct reduction and by plasma reduction? (b) Which are the bottleneck research questions in green steel making? (c) Which oxide and reductant feedstock types can be used in green steel making? ![]() Professor Dierk Raabe, Max-Planck-Institut für Eisenforschung GmbH, Germany
![]() Professor Dierk Raabe, Max-Planck-Institut für Eisenforschung GmbH, GermanyDierk Raabe studied music, metallurgy and metal physics. After his doctorate in 1992 and habilitation in 1997 at RWTH Aachen he received a Heisenberg Fellowship of the German Research Foundation and worked as postdoc at Carnegie Mellon University (Pittsburgh, USA) and at the National High Magnet Field Lab (Tallahassee, USA). He joined the Max Planck Society as a Director in 1999. His interests are in computational materials science, sustainable metallurgy, phase transformation, alloy design, hydrogen and atom probe tomography. He received the Gottfried Wilhelm Leibniz Award of the German Science Foundation, two ERC Advanced Grants and the Acta Materialia Gold Medal Award. He is a Professor at RWTH Aachen in Germany and Honorary Professor at KU Leuven in Belgium. He holds an honorary doctorate degree of the Norwegian University of Science and Technology in Trondheim and is a member of the German National Academy Leopoldina. |
14:45-15:00 |
Discussion
|
15:00-15:30 |
Break
|
15:30-16:00 |
Matching metal supply and demand when electricity and carbon storage are constrained
The carbon emissions of global steel and aluminium production dwarf those of all other metals. The emissions of both primary and recycled aluminium production are already largely a function of the emissions of electricity generation. Although the addition of carbon capture and storage technologies to blast furnaces has been much discussed, it has not developed at any scale, and steel industry plans for decarbonisation now rest largely on the electrical processes of green hydrogen primary production, or recycling in electric arc furnaces. Emissions free metal production therefore depends fundamentally on the availability of emissions free electricity. However, it is very unlikely that sufficient supplies will be available, both due to constraints on the rate of capacity expansion and due to competition with other newly electrified users. As a result, the transition to zero-emissions metals production will face constrained metal production, driving higher prices and motivating new product designs and production processes to make better use of less metal. Building on a recently completed catalogue of global uses of steel and aluminium ordered by component geometry, this paper explores the limits to which we can reduce supply while matching anticipated demand for products. How much less metal can we use? Opportunities to reduce metal use are explored by identifying three forms of scrap: manufacturing scrap, with typically 30-50% of cast metal cut off before final component installation; selection scrap, where largely for economic reasons, designers over-specify components to save design time, exploit economies of scale or as an indicator of product luxury; component scrap, where the full potential of metals properties is not used in current designs, as for example with any component loaded in bending. Case studies of current practice are used to estimate these three scrap rates across the catalogue of component types, and the results are used to motivate changed design practices and innovations in both design and production to use less metal. ![]() Dr Julian Allwood, University of Cambridge, UK
![]() Dr Julian Allwood, University of Cambridge, UKJulian Allwood leads the Low Carbon and Materials Processing research group in the Department of Engineering at the University of Cambridge. The first 10 years of his career were funded by contracts with the Alcoa Technical Centre in Pittsburgh. In 1996 he was appointed as a lecturer in mechanical engineering at Imperial College, and moved to Cambridge in 2000. His research group, currently 15 people, focuses on the technologies and systems of energy, material and resource efficiency, largely related to metals. Current projects include exploration of material efficiency in metals, development of novel metal forming processes, technologies for toner print removal to allow paper-reuse, identification and evaluation of options for future carbon emissions reductions in consumer goods, and development of an online tool for visualising future global and regional resource scenarios. He is a vice Chairman of the International Academy of Production Engineering (CIRP), and since 2007 has been joint editor-in-chief of the Journal of Materials Processing Technology. He has been appointed as a Lead Author for the chapter on mitigation in industry in the IPCC’s 5th Assessment Report, to be published in 2014. In 2008 he was awarded a 5-year £1.4m EPSRC Leadership Fellowship to lead a major project on the global carbon emissions targets for steel and aluminium in collaboration with a consortium of 20 global companies spanning the metals supply chain. This has led to the book “Sustainable Materials: with both eyes open” co-authored with Jonathan Cullen, published by UIT press in 2011. |
16:00-16:15 |
Discussion
|
16:15-17:00 |
Panel discussion
|